Choosing the right anode material is crucial in many applications, from preventing costly corrosion on ships and pipelines to powering the devices we use every day. Whether you’re dealing with sacrificial anodes protecting vital infrastructure or selecting materials for lithium-ion batteries, understanding the properties and functions of different anode types is key. This article delves into the world of anodes, exploring what they are, how they differ from cathodes, the science behind sacrificial anodes, comparing common materials like zinc anodes, aluminum anodes, and magnesium anodes, and even touching upon advanced anode materials like graphite used in modern batteries. If you rely on metal structures in corrosive environments or work with energy storage systems, understanding the best material to use for your anode can save you time, money, and ensure operational efficiency. As someone who has spent years in the materials production industry, specifically with graphite products at our factory in China, I, Allen, have seen firsthand the impact of selecting the appropriate anode material.
What Exactly is an Anode and How Does it Differ from a Cathode?
In the realm of electrochemistry, understanding the fundamental roles of the anode and cathode is essential. These two types of electrodes are the sites where electrochemical reactions occur in devices like batteries or during processes like corrosion protection. The anode is defined as the electrode where oxidation happens – meaning it loses electrons. Conversely, the cathode is the electrode where reduction occurs – it gains electrons. Think of it like a one-way street for electrons: they flow away from the anode, travel through an external circuit (like a wire or the metal being protected), and flow into the cathode.
This distinction between anode and cathode is critical. In a battery providing power (discharging), the negative electrode is the anode, and the positive electrode is the cathode. However, when charging a rechargeable battery, the roles reverse based on the direction of electron flow forced by the charger. In the context of corrosion prevention (which we’ll discuss more), the anode is the metal that sacrificially corrodes, while the cathode is the metal being protected. Understanding this fundamental difference is the first step in selecting the correct anode material for any given application, whether it’s a simple galvanic corrosion scenario or a complex Li-ion battery system. The anode effectively gets ‘consumed’ or changes chemically as it gives up electrons.
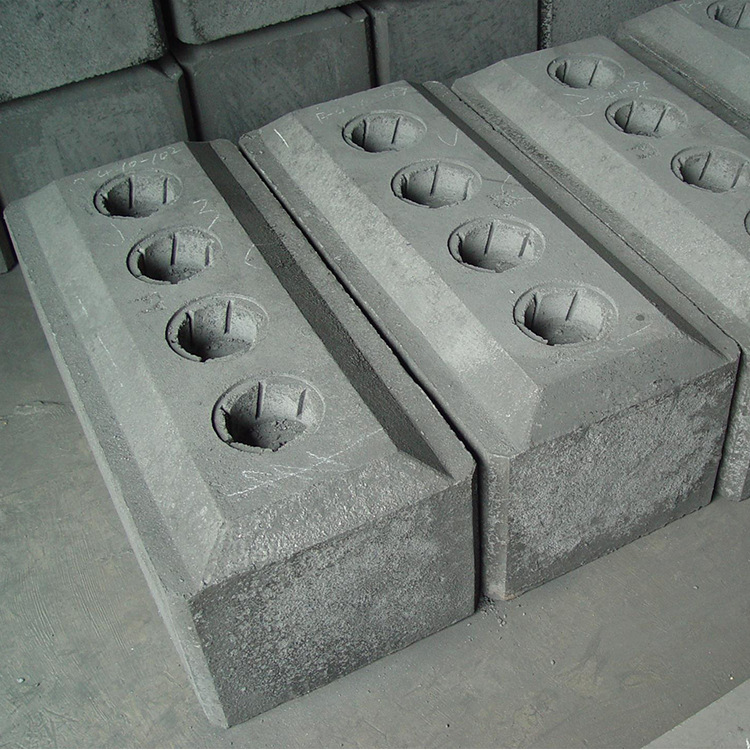
Why is Understanding the Electrode Potential Crucial?
The concept of electrode potential (also known as reduction potential or oxidation potential) is the key to understanding why certain metals act as anodes relative to others. Every metal and conductive material has an inherent tendency to gain or lose electrons when immersed in an electrolyte (a conductive solution, like salt water or battery acid). This tendency is quantified as its electrode potential, typically measured in volts (voltage). When two different metals are electrically connected in an electrolyte, the one with the more negative (or less positive) electrode potential will become the anode – it has a stronger tendency to lose electrons (oxidize). The metal with the more positive potential becomes the cathode.
This difference in electrical potential is the driving force behind galvanic corrosion and the operation of galvanic cells (simple batteries). The larger the difference in potential between the two metals, the stronger the driving force for electron flow and the faster the anode will corrode or react. For example, magnesium has a very negative potential compared to steel, making it a highly effective, albeit faster-consuming, anode for protecting steel. Understanding these potential values allows engineers and procurement specialists like Mark Thompson to predict which metal will be the anode and which will be the cathode in a given system, enabling the design of effective cathodic protection systems or efficient batteries. The voltage potential difference directly impacts the rate of the oxidation reaction at the anode.
What is a Sacrificial Anode and How Does it Work?
A sacrificial anode is a core component in a common method of corrosion control called cathodic protection. The basic idea is simple yet ingenious: you intentionally introduce a piece of metal that is more easily corroded (more reactive, meaning it has a more negative electrode potential) than the metal structure you want to protect. This "sacrificial" metal becomes the anode in the electrochemical cell created, while the structure you’re protecting (like a ship’s hull, pipeline, or water heater tank) becomes the cathode.
How does this protect anything? When corrosion conditions exist (typically involving a metal, an electrolyte like salt water or even moist soil, and an electrical connection), the sacrificial anode preferentially corrodes, losing electrons and dissolving over time. These electrons flow through the electrical connection (often the structure itself) to the cathode (the protected metal), where they participate in reduction reactions (often involving dissolved oxygen or water). By forcing the protected structure to become the cathode, you prevent it from losing its own electrons and thus prevent it from corroding. This is the essence of cathodic protection: the sacrificial anode gives itself up to save the more valuable or critical metal structure. The effectiveness relies entirely on the anode material having a significantly lower potential than the metal being protected. This is a prime use as a sacrificial anode.
Zinc Anode vs. Aluminum Anode: Which is Better for Salt Water?
When it comes to protecting steel and other metals in salt water environments, zinc anodes and aluminum anodes are the two most common choices for sacrificial anodes. Both have distinct advantages and disadvantages. Zinc anodes, often made from a specific alloy meeting military specifications (Mil-Spec), have been the traditional choice for decades. They provide a reliable, steady potential difference relative to steel, offer good capacity (amount of charge delivered per unit weight), and tend to corrode evenly. Their primary drawback is their lower voltage potential compared to aluminum or magnesium, meaning they might not provide sufficient protection in less conductive environments like brackish water or if the coating on the protected structure is damaged.
Aluminum anodes, typically specific aluminum alloys containing indium and zinc to prevent passivation (forming a protective oxide layer that stops operation), offer several advantages. They generally have a higher electrical potential difference against steel than zinc anodes, providing potentially stronger protection. Critically, they also have a significantly higher capacity per pound – meaning an aluminum anode of the same weight as a zinc anode can theoretically last longer or provide more protective current. This makes them attractive for applications where weight or replacement frequency is a concern. However, quality control is crucial for aluminum anodes; poorly made ones can passivate and become ineffective. For typical saltwater applications, modern aluminum alloys are often preferred due to their higher capacity, but zinc anodes remain a reliable, time-tested option. The choice between zinc and aluminum often comes down to specific operating conditions and cost-benefit analysis.
When Should Magnesium Anodes Be Used?
While zinc anodes and aluminum anodes dominate salt water applications, magnesium anodes carve out their niche primarily in fresh water. Magnesium is the most reactive of the common sacrificial anode materials, meaning it has the most negative electrode potential (around -1.6V to -1.75V compared to Ag/AgCl reference, versus roughly -1.05V for zinc and -1.1V for typical aluminum alloy anodes). This high potential difference makes magnesium anodes exceptionally effective at providing cathodic protection, especially in electrolytes with higher electrical resistance, like fresh water.
Because fresh water is less conductive than salt water, the higher driving voltage of magnesium anodes is often necessary to push enough protective current to the cathode (the structure being protected, like a water heater tank or a boat in fresh water). However, this high reactivity comes at a cost. Magnesium anodes corrode much faster than zinc or aluminum anodes in any environment, especially in salt water where they might overprotect and potentially cause coating damage (hydrogen evolution). Their lower capacity (amp-hours per pound) compared to aluminum also means they need to be replaced more frequently. Therefore, magnesium anodes are the go-to choice for fresh water applications but are generally unsuitable or less economical for saltwater use.
Can Other Metals Act as Anodes?
Yes, absolutely. The designation of a metal as an anode or cathode is relative. Any metal can potentially act as an anode if it is electrically coupled to a more noble metal (a metal with a more positive electrode potential) in the presence of an electrolyte. For example, steel will act as an anode and corrode if connected to stainless steel or copper in salt water. Iron is anodic to nickel. This is the principle behind galvanic corrosion – the undesirable corrosion that occurs when dissimilar metals are in contact.
However, when we talk about anode materials for practical applications like cathodic protection or batteries, we specifically choose materials that have desirable properties for that role. For sacrificial anodes, we want metals like zinc, aluminum, or magnesium because they have a significantly more negative potential than common structural metals like steel, providing a strong protective effect. We also consider factors like cost, capacity, how evenly they corrode, and environmental impact. While technically many metals can be anodes, only a few are suitable and cost-effective for widespread use as a sacrificial anode or as high-performance electrode components in batteries. The formation of stable metal oxides can sometimes passivate a potential anode, rendering it ineffective unless specific alloying elements are added, as seen in aluminum alloys designed for anodic protection.
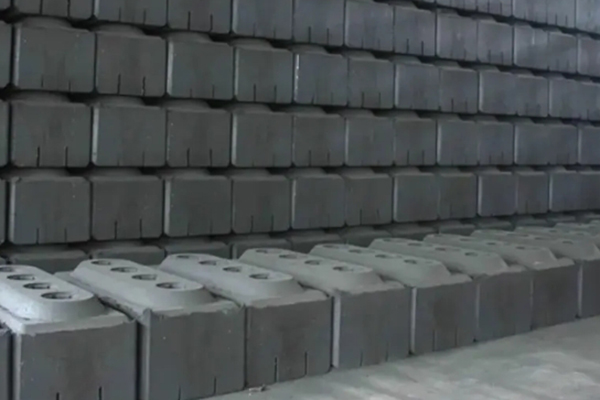
What are the Key Materials for Lithium-Ion Battery Anodes?
Shifting from corrosion protection to energy storage, the anode plays a critical role in materials for lithium-ion batteries. In a typical Li-ion battery, the anode (the negative electrode during discharge) is the electrode that absorbs lithium ions (ion) when the battery is charging and releases them when it’s discharging. The choice of anode material significantly impacts the battery’s capacity (how much energy it can store), charging speed (high rate capability), lifespan, and safety.
The most dominant anode material by far is graphite. Why graphite? Graphite, a form of carbon, has a layered structure that allows lithium ions to slide in between the layers (a process called intercalation) during charging and slide back out during discharging (lithiation and delithiation). High purity 99.9% graphite powder and specially processed graphitic materials offer several advantages:
- Good specific capacity (around 372 mAh/g theoretically).
- Excellent cycle life (can withstand many charge and discharge cycles).
- Relatively low cost and abundance.
- Stable voltage profile.
Other anode materials are being actively researched and developed to overcome graphite‘s limitations (primarily its theoretical capacity). These include:
- Silicon (Si): Offers much higher theoretical capacity (over 3000 mAh/g) but suffers from massive volume expansion during intercalation, leading to rapid degradation. Often used in blends with graphite.
- Lithium Titanate (LTO): Provides exceptional cycle life and safety, and allows for very fast charging, but has lower capacity and higher cost.
- Graphene and other carbon materials: Explored for potentially faster charging and improved conductivity. Graphene, a single layer of graphite, shows promise.
- Metal Oxides: Certain metal oxides are also being investigated as anode materials.
Anode materials must be able to efficiently host lithium ions without significant structural damage over many cycles. The development of advanced carbon-based and silicon-based anodes is crucial for next-generation energy storage systems, including those for hybrid electric vehicles (HEV) and grid-scale energy storage.
How Does the Cathode Material Influence Battery Performance?
While this article focuses on the anode, it’s impossible to discuss battery performance without acknowledging the crucial role of the cathode material. The cathode (the positive electrode during discharge) is the electrode that releases lithium ions during charging and accepts them during discharging. The cathode material largely determines the battery’s voltage, overall capacity (specific energy and power), cost, and safety characteristics.
Common cathode materials are typically lithium metal oxides. Some key examples include:
- Lithium Cobalt Oxide (LiCoO2 or LCO): Found in many consumer electronics due to its high energy density. However, cobalt-based materials raise cost and ethical sourcing concerns, and LCO has safety limitations. Cobalt oxide itself is a key component.
- Lithium Nickel Manganese Cobalt Oxide (NMC): A popular choice for electric vehicles, offering a balance of energy, power, lifespan, and improving safety compared to LCO. The ratio of nickel, manganese, and cobalt can be tuned for different properties.
- Lithium Iron Phosphate (LFP): Known for its excellent safety, long cycle life, and lower cost (no cobalt). Its main drawback is lower voltage and energy density compared to NMC or LCO, though this is improving.
- Lithium Nickel Cobalt Aluminum Oxide (NCA): Used by some EV manufacturers, offering high energy density but requiring careful thermal management.
The interaction between the anode material (like graphite) and the cathode material within the electrolyte dictates the overall performance of the Li-ion battery. Researchers are constantly seeking new materials for the cathode that offer higher capacity, better safety, longer life, faster charge-discharge capabilities, and lower cost, often focusing on reducing or eliminating expensive or problematic elements like cobalt. The synergy between anode and cathode development is key to advancing battery technology. Both positive electrode and negative electrode materials are critical.
What Factors Determine the Best Material to Use for an Anode?
Selecting the best material to use for an anode isn’t a one-size-fits-all decision. The optimal choice of anode depends heavily on the specific application and operating environment. Key factors include:
-
Electrochemical Potential:
- Sacrificial Anodes: The anode material must have a significantly more negative potential than the metal being protected to provide adequate driving voltage for cathodic protection. The required potential difference depends on the electrolyte‘s conductivity (salt water vs. fresh water).
- Battery Anodes: The anode potential affects the overall cell voltage. A lower anode potential (relative to lithium) generally leads to a higher cell voltage and thus higher energy density.
-
Capacity:
- Sacrificial Anodes: Higher capacity (Amp-hours per kilogram or per volume) means the anode will last longer or a smaller/lighter anode can be used. Aluminum alloys generally offer the highest capacity among common sacrificial materials.
- Battery Anodes: Higher specific capacity (mAh per gram) means the battery can store more energy for a given weight/size. This is a major driver for research into materials like silicon.
-
Operating Environment:
- Sacrificial Anodes: Conductivity (salt water, brackish, fresh water, soil), temperature, and flow rate all influence anode performance and consumption rate. Magnesium excels in fresh water, while zinc and aluminum are better suited for saltwater.
- Battery Anodes: Temperature range, required charge and discharge rates, and safety considerations influence the choice (e.g., LTO for high power and safety).
-
Efficiency and Consumption Pattern:
- Sacrificial Anodes: Ideally, the anode should corrode evenly and efficiently without passivation (oxide layer formation) or excessive self-corrosion.
- Battery Anodes: Efficiency relates to minimizing irreversible capacity loss during cycling. Uniform intercalation/de-intercalation is crucial for longevity.
-
Cost and Availability: The cost-effectiveness of the anode material and its manufacturing process is always a major consideration, especially for large-scale applications like marine protection or grid-scale energy storage. Graphite‘s relative abundance contributes to its dominance in Li-ion batteries.
-
Mechanical Properties and Form Factor: The anode material must be manufacturable into the required shapes (e.g., hull anodes, bracelet anodes for pipelines, electrode coatings for batteries). For instance, high strength graphite blocks demonstrate the ability to form robust structures from graphite.
Considering these factors allows for the selection of the most appropriate anode material to achieve the desired performance, lifespan, and cost-effectiveness.
Why is Quality Control So Vital in Anode Materials Production?
As someone overseeing materials production in a factory with 7 production lines, specializing in products like ultra-high power graphite electrodes, I cannot overstate the importance of rigorous quality control, especially for anode materials. Whether it’s a sacrificial anode or a battery electrode, inconsistent quality can lead to premature failure, inadequate performance, safety hazards, and significant financial losses for the end-user – concerns often raised by discerning buyers like Mark Thompson.
For sacrificial anodes (zinc anode, aluminum anode, magnesium anodes), quality control ensures:
- Correct Alloy Composition: Even small variations in the alloy used can drastically alter the anode‘s potential, capacity, and susceptibility to passivation. Impurities can reduce efficiency or cause uneven corrosion.
- Consistent Performance: Users rely on anodes to provide predictable protection over their expected lifespan. Poor quality control leads to unpredictable degradation and potential failure of the cathodic protection system, leaving expensive assets vulnerable to corrosion.
- Reliable Activation: Particularly for aluminum anodes, proper manufacturing prevents the formation of passive oxide layers that can insulate the anode and render it useless.
- Accurate Certifications: Reputable manufacturers provide verifiable certifications (e.g., ISO standards, material specifications) confirming the anode material meets required standards. This builds trust and avoids issues like certificate fraud, a known pain point for buyers.
For battery anode materials like graphite:
- Purity: Impurities can cause side reactions, reducing battery life and potentially creating safety issues.
- Particle Size and Morphology: The physical characteristics of the graphite powder (nanoparticle size, shape, surface area) directly impact lithiation kinetics, influencing charging speed and power density. Consistency is key.
- Structural Integrity: Defects in the graphitic structure can hinder intercalation and lead to faster degradation during charge and discharge cycles.
Ultimately, stringent quality control in anode materials production translates to reliability, safety, and predictable performance. This involves careful raw material selection, precise process control (mixing, casting, heat treatment, graphitization), and thorough testing (chemical analysis, electrochemical testing, long-term test protocols). For buyers sourcing these critical components, partnering with a manufacturer who prioritizes and can demonstrate robust quality control is paramount to avoiding costly failures and ensuring operational success. Our commitment at the Professional Graphite Electrode Factory is built on this foundation of quality.
Key Takeaways on Anode Materials:
- The anode is the electrode where oxidation (loss of electrons) occurs, while the cathode is where reduction (gain of electrons) occurs.
- Electrode potential dictates which metal becomes the anode in a galvanic couple; the one with the more negative potential corrodes preferentially.
- Sacrificial anodes (zinc anode, aluminum anode, magnesium anode) protect more valuable metals (cathode) by corroding instead, a process called cathodic protection.
- Zinc anodes are reliable in salt water; aluminum anodes offer higher capacity in salt water but require careful quality control; magnesium anodes provide high potential ideal for fresh water but corrode quickly.
- Graphite is the dominant anode material in Li-ion batteries due to its good capacity, cycle life, and cost, enabling lithium ion storage via intercalation.
- Silicon and other advanced materials (graphene, LTO, metal oxides) are being developed as anode materials for higher capacity or faster charging.
- The cathode material (often lithium metal oxides like LCO, NMC, LFP) significantly impacts battery voltage, capacity, safety, and cost.
- Choosing the best material to use for an anode depends on potential, capacity, environment (salt water vs. fresh water), cost, and required lifespan.
- Strict quality control during anode materials production is essential for ensuring consistent performance, preventing premature failure (corrosion, degradation), and guaranteeing safety in both sacrificial anode and battery applications.
Post time: 04-11-2025