Electric arc furnace (EAF) technology stands as a cornerstone of modern steelmaking, offering flexibility and efficiency, particularly in recycling scrap steel. At the very heart of this powerful process are the graphite electrodes. These aren’t just simple rods; they are highly engineered consumables critical for delivering the immense electrical energy needed to melt scrap and produce steel. Understanding the function, types, quality factors, and proper handling of these electrodes is crucial for any electric arc furnace operator, foundry manager, or procurement specialist like Mark Thompson aiming for optimal performance and cost-effectiveness. This article delves deep into the world of arc furnace electrodes, explaining why graphite is the material of choice, how the arc works its magic within the furnace, what defines a quality electrode, and how partnering with a knowledgeable manufacturer like us, with 7 production lines right here in China, can safeguard your operations. We’ll explore everything from the raw materials to the final steelmaking process, ensuring you have the insights needed to make informed decisions.
What Exactly is an Electric Arc Furnace (EAF) and How Does it Melt Steel?
An Electric Arc Furnace, often abbreviated as EAF, is a type of furnace that heats charged material primarily by means of an electric arc. Think of it as a giant kettle, but instead of heating water, it melts tons of scrap steel and other metallic inputs using incredibly high temperatures generated by electricity. These furnaces are workhorses in the steel industry, especially favoured for their ability to efficiently recycle scrap metal, making the steelmaking process more sustainable compared to traditional blast furnaces that rely heavily on iron ore. The basic structure involves a refractory-lined vessel (the furnace shell), a roof with ports for the electrodes, and a tapping spout to pour out the molten steel.
The process starts by loading the furnace with scrap steel (the primary feedstock) and sometimes other raw materials like direct reduced iron (DRI) or pig iron. Once loaded, the roof is swung into place, and the graphite electrodes are lowered towards the scrap. An extremely high electric current passing through the electrode creates powerful electric arcs between the electrode tips and the metallic charge. This arc generates intense heat, reaching temperatures that can exceed 3,000 degrees Celsius (approaching 5000 degrees Fahrenheit in the arc itself), which rapidly melts the scrap steel. The entire furnace often sits on a tilting platform to allow for the pouring of the molten steel once the desired temperature and chemistry are achieved. EAFs are versatile, capable of producing a wide range of steel grades.
The efficiency and speed of the electric arc furnace have made it a dominant technology in steelmaking worldwide. Unlike induction furnaces which use eddy currents to heat the metal, the EAF uses the direct heat of the electric arc to melt the charge. This direct application of electrical energy allows for rapid melting cycles. The furnace itself must be robust, with the shell typically lined with refractory materials like refractory brick to withstand the extreme conditions. Modern EAFs incorporate advanced control systems, water-cooled panels for the walls and roof, and sophisticated mechanisms for handling the electrodes and managing the melt.

How Do Graphite Electrodes Generate the Intense Heat Needed in an EAF Furnace?
The magic of the electric arc furnace lies in the electric arc itself, and the graphite electrodes are the conduits that make it happen. Typically, three electrodes are used in an AC (alternating current) furnace, arranged in a triangular pattern. These cylindrical columns of graphite act as terminals for a high-power electrical supply, connected via large water-cooled cables. When the electrodes are lowered close to the metallic charge (scrap steel) inside the furnace, a high voltage is applied. This voltage ionizes the air (or gases) in the gap between the electrode tip and the scrap, creating a conductive path.
Once this path is established, a massive electric current (tens of thousands of amperes) flows through the electrodes and jumps across the gap, forming a sustained electric arc. This arc is essentially a continuous, high-temperature plasma discharge. It converts electrical energy into thermal energy with incredible efficiency, releasing tremendous heat directly onto the scrap metal. It’s this focused, intense heat from the arc (or arcs, in a three-electrode setup) that does the heavy lifting, rapidly melting the scrap and forming a molten pool. The electrodes are precisely controlled to maintain the optimal arc length and stability throughout the melting process.
The power delivered through the electrodes is immense. Think about the energy required to melt tons of solid steel in under an hour – that’s the scale we’re operating at. The electrodes themselves get consumed during this process due to oxidation at their tips and sublimation in the extreme heat of the arc, but their primary function is to conduct the necessary current and sustain the arc required to heat and melt the charge efficiently. The stability and intensity of the arc directly impact the furnace‘s productivity and energy consumption, highlighting the critical role of the electrode system.
Why is Graphite the Unrivaled Material for Arc Furnace Electrodes?
The conditions inside an electric arc furnace are incredibly demanding. Temperatures soar, electrical currents are enormous, and thermal shock is intense. So, why graphite? Why not copper or tungsten? The answer lies in graphite‘s unique combination of properties, making it ideally suited for service as an electrode in these extreme environments. As a manufacturer, we rely heavily on these inherent characteristics.
Firstly, graphite has exceptionally high thermal conductivity and excellent resistance to thermal shock. This means it can withstand the rapid temperature changes experienced when the arc strikes and during the melting process without easily cracking or failing. Graphite can withstand temperatures far exceeding the melting point of steel. Secondly, graphite maintains its mechanical strength remarkably well at very high-temperature levels, unlike most metals which weaken significantly. This structural integrity is vital for the long electrode columns used in large furnaces.
Thirdly, and crucially for an electrode, graphite has low electrical resistance (or high electrical conductivity). This allows it to carry the massive currents required for the arc without excessive internal heating (heat loss) or voltage drop. Its low resistivity ensures efficient energy transfer to the melt. Fourthly, graphite has a very high sublimation point (it turns directly from solid to gas) rather than a low melting point. While electrode consumption through oxidation and sublimation does occur, graphite‘s ability to endure these conditions is far superior to other potential materials. The manufacturing process, involving graphitization at extremely high temperatures, aligns the carbon structure to optimize these thermal and electrical properties. It’s this blend of thermal resilience, high-temperature strength, and electrical conductivity that makes graphite the indispensable material for arc furnace electrodes.
What Different Grades of Graphite Electrode Exist for Steelmaking Furnaces? (UHP, HP, RP Explained)
Not all electric arc furnaces are created equal, and neither are the graphite electrodes they use. The demands placed on an electrode vary significantly depending on the furnace‘s power rating, operating practices, and the type of steel being produced. To meet these varying needs, graphite electrodes are used in different grades, primarily classified by their current-carrying capacity and physical properties. As a factory like ours, we produce a range of these to cater to diverse customer requirements.
The main grades for arc furnace electrodes include:
- Regular Power (RP): These electrodes are designed for lower-powered electric arc furnaces, typically those used in foundries or for less demanding steelmaking operations. They use standard quality petroleum coke and have moderate current density capabilities.
- High Power (HP): HP electrodes offer better performance than RP grades. They are made using higher quality petroleum coke and can handle higher current densities. These are suitable for electric arc furnaces involved in standard steelmaking and refining operations. You can explore options like our High-power graphite electrode for reliable performance in these applications.
- Ultra-High Power (UHP): These are the top-tier electrodes, engineered for the most demanding electric arc furnace applications. UHP electrodes are manufactured using premium needle coke, which provides superior structure, lower electrical resistance, higher density, and better resistance to thermal shock and oxidation. They can withstand extremely high current densities, making them essential for large, high-productivity EAFs used to make steel rapidly and efficiently. Our Ultra-high power graphite electrode is specifically designed for these challenging environments. For the largest furnaces, specialized Extra Large Graphite Electrode sizes are also available.
The choice of electrode grade directly impacts furnace efficiency, electrode consumption rates, and overall operating costs. Using a lower grade electrode in a high-power furnace leads to rapid consumption and potential breakage, while using a UHP electrode in a low-power furnace might be unnecessarily expensive. Matching the electrode grade to the furnace requirements is key for optimal EAF steelmaking.
Can You Explain the Journey: How is a High-Quality Graphite Electrode Manufactured?
Creating a graphite electrode capable of performing reliably in an electric arc furnace is a complex, multi-stage process that demands precision and careful control over raw materials and processing parameters. As manufacturers, we oversee this journey meticulously. It begins with selecting the right carbonaceous raw materials, primarily high-quality petroleum coke (especially needle coke for UHP electrodes) and coal tar pitch as a binder.
The process typically involves these key steps:
- Mixing: The calcined coke particles are carefully sized and mixed with molten coal tar pitch. The proportions and mixing quality are critical for the final electrode properties.
- Forming (Extrusion or Molding): The heated paste-like mixture is then formed into the desired cylindrical shape, usually through extrusion for standard sizes or molding for very large electrodes or specialized shapes. This forms a "green" electrode.
- Baking: The green electrodes are slowly heated in large baking furnaces over several weeks to temperatures around 800-1000 degrees Celsius. This process carbonizes the pitch binder, creating a solid carbon structure and driving off volatile materials. Careful temperature control is essential to prevent cracking.
- Impregnation (Optional but common for HP/UHP): To increase density and strength, baked electrodes are often impregnated with liquid pitch under pressure and then re-baked. This fills internal pores.
- Graphitization: This is the most critical and energy-intensive step. The baked electrodes are heated in specialized electric furnaces (like Acheson furnaces) to extremely high temperatures, typically between 2500 and 3000 degrees Celsius. This intense heat transforms the amorphous carbon structure into crystalline graphite. This graphitization step is what imparts the excellent thermal and electrical conductivity required for EAF electrodes.
- Machining: After cooling, the graphitized electrodes are precision-machined to exact dimensions. This includes cutting them to length and creating threaded sockets at each end. These sockets allow individual electrodes to be joined together using connecting pins (nipples), also made of graphite, to form long columns that reach into the furnace. The precision of the thread is vital for strong, low-resistance joints.
Throughout this process, rigorous quality control checks are performed, from raw material analysis to final inspection of the machined electrode. It’s a journey from carefully selected raw materials to a highly engineered product designed to withstand the punishing environment of an electric arc furnace.
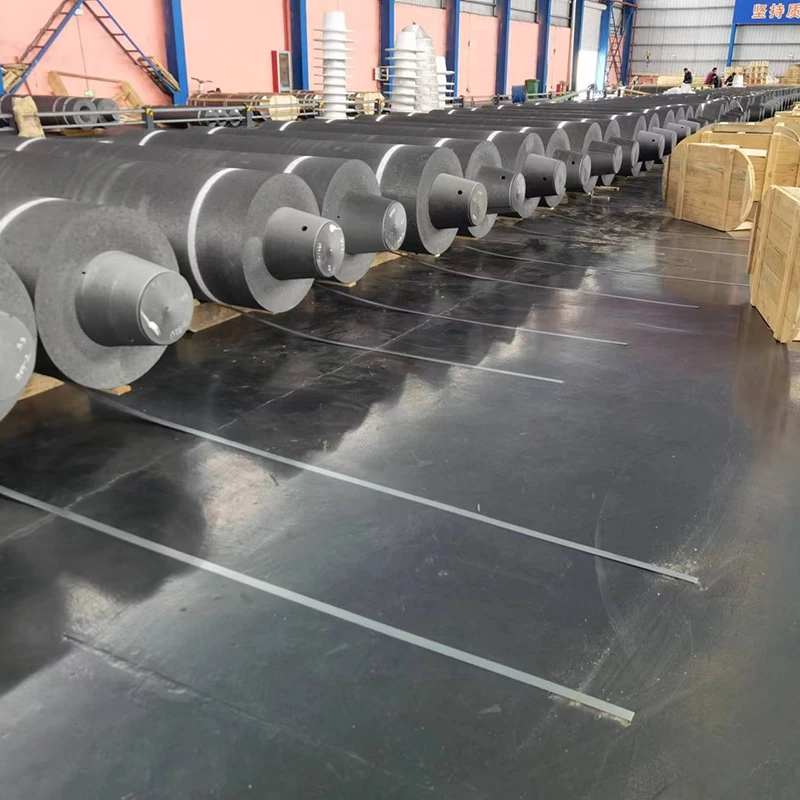
What Critical Quality Checks Ensure Electrode Performance During the Furnace Melt?
For steelmakers like Mark Thompson, consistent electrode performance is paramount. Unforeseen failures or high consumption rates can disrupt production schedules and significantly increase costs. Therefore, ensuring the quality of graphite electrodes is not just a checkbox exercise; it’s fundamental to reliable electric arc furnace operation. At our factory, quality control is integrated into every stage, from raw material sourcing to final shipment.
Key quality aspects we focus on include:
- Raw Material Quality: Verifying the properties of incoming petroleum coke and pitch binder. Needle coke quality is especially critical for UHP electrodes.
- Dimensional Accuracy: Ensuring the electrode diameter, length, and crucially, the precision of the machined sockets and connecting nipples (thread accuracy) meet strict tolerances. Poorly fitting joints increase electrical resistance and are prone to failure.
- Physical Properties: Testing samples from each production batch for critical properties like:
- Apparent Density: Higher density generally indicates better quality and lower consumption.
- Electrical Resistivity: Lower resistivity means better conductivity and less power loss within the electrode. This is vital for thermal efficiency.
- Flexural Strength & Modulus of Elasticity: These indicate the electrode‘s mechanical strength and resistance to bending forces during handling and operation in the furnace.
- Coefficient of Thermal Expansion (CTE): Low CTE helps the electrode withstand thermal shock.
- Ash Content: Low ash content is desirable to minimize impurities introduced into the steel melt.
- Structural Integrity: Using non-destructive testing methods (like ultrasonic testing) to check for internal cracks or flaws that could lead to premature failure under stress or heat within the electric arc furnace.
- Certification and Traceability: Providing comprehensive test reports and certifications (e.g., ISO 9001 compliance, material specification sheets) for each batch, ensuring full traceability from production to delivery. Addressing concerns about certificate fraud requires transparency and robust documentation from the supplier.
These checks collectively ensure that the electrodes supplied can handle the specified electrical load, resist the harsh furnace environment (intense heat, thermal shock, mechanical stress), and provide predictable consumption rates, allowing steelmakers to operate their EAFs efficiently and reliably.
How are Electrodes Properly Handled and Integrated into the Electric Arc Furnace Operation?
Even the highest quality graphite electrode can fail if not handled and used correctly. Given their size, weight, and relative brittleness compared to metals, proper procedures are essential to prevent damage and ensure operational safety and efficiency within the steel mill. We always advise our clients on best practices.
Handling involves carefully lifting electrodes using designated slings or clamps, avoiding impacts that could cause cracks. Storage should be in a clean, dry area, protected from mechanical damage. When preparing an electrode column, the threaded sockets of the electrode and the nipple must be thoroughly cleaned to remove any dust or debris, which could increase electrical resistance at the joint. Applying the correct torque when tightening the joint is critical – under-tightening leads to high resistance and overheating, while over-tightening can damage the threads or electrode structure. Specialized torque wrenches are used for this.
Once assembled into columns, the electrodes are mounted onto the electrode arms of the electric arc furnace. These arms, connected to the power supply via large water-cooled cables, allow the electrodes to be raised, lowered, and swung aside for charging the furnace. During operation, the electrode regulation system automatically adjusts the position of each electrode to maintain a stable arc and control power input. The electrodes are lowered progressively as the scrap melts down and as the electrode tips are consumed. Operators monitor electrode performance, looking for signs of excessive consumption, tip splitting, or joint problems. Careful operation helps maximize electrode life and maintain consistent heat input to the melt.
What Common Issues Arise with Electrodes During the Melt Process and How Can They Be Mitigated?
Despite being robust, graphite electrodes operate at the limit of material endurance within the electric arc furnace. Several issues can arise during the demanding melt cycle, impacting efficiency and cost. Understanding these helps operators and procurement managers like Mark make better choices and troubleshoot problems.
- High Consumption: This is the most common concern. Consumption occurs through:
- Tip Sublimation: Carbon vaporizing directly from the tip in the extreme heat of the arc.
- Oxidation: Carbon reacting with oxygen in the furnace atmosphere along the sidewalls of the electrode. This is often the largest component of consumption.
- Breakage: Mechanical failure of the electrode column or joint.
- Mitigation: Using the correct electrode grade (e.g., UHP for high power), optimizing furnace sealing to reduce air ingress (minimizing oxidation), maintaining proper joint tightness, ensuring stable arc regulation, and sometimes using protective coatings or water-cooled spray rings can help manage consumption.
- Breakage: Sudden electrode failure is disruptive and costly. Causes include:
- Thermal Shock: Rapid temperature changes, especially during startup or if water leaks occur.
- Mechanical Stress: Non-conductive material falling from the roof, excessive vibrations, or scrap collapses impacting the electrode.
- Poor Joint Assembly: Incorrect torque or dirty threads leading to overheating and joint failure.
- Internal Defects: Manufacturing flaws (though rigorous QC minimizes this).
- Mitigation: Careful scrap management, proper joint assembly, pre-heating electrodes if necessary, regular furnace maintenance, and using high-quality electrodes with good mechanical strength and thermal shock resistance.
- Tip Splitting/Cracking: Can occur due to rapid heating/cooling cycles or inconsistencies in electrode structure. High-quality, homogenous electrodes are less prone to this.
- High Electrical Resistance: Often caused by loose or dirty joints, leading to overheating, increased energy consumption, and potential joint failure. Regular cleaning and correct torquing are essential.
Addressing these issues involves a combination of using the right quality graphite electrode, implementing best operational practices within the steel mill, and maintaining the electric arc furnace properly. Efficient communication between the electrode supplier and the furnace operator is also key to diagnosing and solving problems.
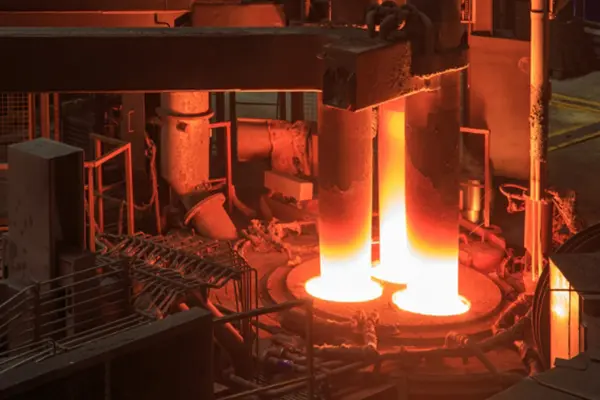
How Can Steel Mills Like Yours Select a Reliable Graphite Electrode Supplier?
For Mark Thompson and other procurement professionals, choosing the right graphite electrode supplier is a critical decision with significant operational and financial implications. Finding a partner who provides consistent quality, competitive pricing, reliable delivery, and excellent support is vital. Mark’s pain points – inefficient communication, shipment delays, and certificate fraud – highlight the importance of due diligence. Here’s what I, Allen, recommend focusing on, based on our experience as a long-term supplier to markets like the USA, Europe, and Australia:
- Proven Manufacturing Expertise: Look for established factories with dedicated production lines (like our 7 lines) and a history of producing the specific grades (UHP, HP, RP) you need. Experience matters in mastering the complex graphite electrode manufacturing process. Visiting the factory, if possible, or attending major industry exhibitions where suppliers showcase their capabilities can provide valuable insights.
- Robust Quality Management System: Insist on suppliers with verifiable quality certifications (ISO 9001 is standard). Ask detailed questions about their quality control procedures, from raw material inspection (coke analysis) to final product testing (resistivity, strength, density, dimensions). Request sample test reports and understand their process for ensuring batch-to-batch consistency. Don’t just accept a certificate; inquire about the underlying processes it represents. This helps combat potential certificate fraud.
- Technical Support and Communication: A good supplier acts as a partner, not just a vendor. Evaluate their technical team’s knowledge. Can they offer advice on electrode selection, handling, and troubleshooting furnace issues? Is their sales team responsive, knowledgeable (beyond just sales talk), and easy to communicate with (addressing language barriers if applicable)? Efficient communication is crucial, especially when resolving issues quickly.
- Logistics and Reliability: Discuss lead times, shipping options, and their track record for on-time delivery. Shipment delays can halt steelmaking operations, so reliability is key. Understand their packaging methods to prevent damage during transit. Ask about their experience shipping to your country (USA, Europe, etc.) and their familiarity with customs procedures.
- Transparency and Trust: Look for suppliers who are open about their processes and willing to provide detailed information. Building a long-term relationship based on trust is often more valuable than saving a few dollars per electrode with an unknown or unreliable source. Discuss payment methods upfront and ensure they are secure and transparent.
- Competitive Pricing (Value, Not Just Cost): While price is always a factor, focus on the overall value. A slightly cheaper electrode that consumes faster or breaks frequently will cost more in the long run due to lost production and higher consumption per ton of steel. Evaluate pricing in the context of quality, reliability, and support.
Finding suppliers via Google search is common, but supplement this with deeper investigation, reference checks (if possible), and direct engagement, perhaps initially at an exhibition. Prioritize suppliers who understand the demands of electric arc furnace steelmaking and demonstrate a commitment to quality and customer success.
What is the Future Outlook for Graphite Electrodes in Modern Electric Arc Furnace Steelmaking?
The future for graphite electrodes is intrinsically linked to the future of electric arc furnace (EAF) steelmaking. And that future looks bright, driven by several key trends. EAF steelmaking is generally considered more environmentally friendly than traditional blast furnace routes, primarily due to its ability to use high percentages of scrap steel, reducing the need for raw material extraction and lowering CO2 emissions per ton of steel produced. As environmental regulations tighten globally and the push for a circular economy intensifies, the share of steel produced via EAFs is expected to continue growing.
This growth directly translates into sustained demand for high-quality graphite electrodes. Furthermore, the trend is towards larger, more powerful electric arc furnaces (UHP furnaces) to maximize productivity and efficiency. These modern electric arc furnaces require increasingly sophisticated electrodes capable of handling higher currents and stresses, pushing manufacturers like us to continually innovate in materials (like advanced needle coke) and production techniques to improve electrode performance – specifically targeting lower electrical resistance, higher thermal shock resistance, and reduced oxidation rates.
Research also continues into areas like:
- Surface Coatings: Developing better protective coatings to minimize sidewall oxidation, a major factor in electrode consumption.
- Improved Joint Design: Enhancing the thread design and nipple material for even lower resistance and stronger joints.
- Alternative Technologies: While graphite remains dominant, research explores alternative current carriers, though none currently match graphite‘s overall performance profile for large EAFs. Direct Current (DC) furnaces, often using a single large graphite electrode, also represent a segment of the market with specific electrode requirements.
- Smart Furnace Operations: Integrating sensor technology and AI to optimize electrode regulation, power profiles, and predict potential issues, thereby maximizing electrode life and furnace efficiency.
As steelmakers strive to produce high-quality steel more efficiently and sustainably, the demand for reliable, high-performance graphite electrodes will remain strong. We, as manufacturers, are committed to meeting this demand through continuous improvement and innovation, ensuring the electrode remains a key enabler of modern electric arc steelmaking.
Key Takeaways:
- Graphite electrodes are essential consumables in Electric Arc Furnaces (EAFs), conducting high currents to create an arc that melts scrap steel.
- Graphite is the ideal material due to its high heat resistance, good electrical conductivity, thermal shock resistance, and high-temperature strength.
- Electrodes come in grades (RP, HP, UHP) matched to furnace power; UHP electrodes use premium needle coke for maximum performance.
- Manufacturing is complex, involving mixing, forming, baking, graphitization (at ~3000°C), and precision machining.
- Quality control (checking density, resistivity, strength, dimensions) is critical for reliable electrode performance and predictable consumption in the furnace melt.
- Proper handling, storage, and joint assembly (cleaning, correct torque) are vital to prevent electrode damage and ensure efficient operation.
- Common issues include consumption (oxidation, tip loss), breakage (thermal/mechanical stress), and joint problems; mitigation involves quality electrodes and good operating practices.
- Choosing a supplier requires evaluating manufacturing expertise, quality systems, technical support, communication, logistics reliability, and overall value – not just price. Look for transparency and trust.
- The future of EAF steelmaking is strong, driving continued demand and innovation in graphite electrode technology for higher power furnaces and improved efficiency.
Post time: 04-18-2025