Carbon anodes are the unsung heroes of the aluminium industry. They are a critical component in the energy-intensive electrolysis process that transforms alumina into the versatile metal we use everywhere. Understanding their production, function, and quality is paramount for anyone involved in aluminum production, especially procurement professionals like Mark Thompson who navigate the complexities of sourcing these essential materials. This article delves into the world of carbon anodes, exploring the crucial roles of petroleum coke and binders, the intricacies of anode production, their behaviour during aluminum electrolysis, and the key considerations for ensuring a stable, high-quality supply. Reading this will provide valuable insights into optimizing aluminium smelting operations and making informed purchasing decisions.
What Exactly is a Carbon Anode and Why is it Crucial for Aluminum Production?
A carbon anode is essentially a large block made primarily from processed carbonaceous materials, predominantly calcined petroleum coke bonded together with coal tar pitch. In the context of primary aluminum production, its role is absolutely fundamental. It serves as one half of the electrochemical cell (specifically, the positive electrode or anode and cathode pair) used in the Hall-Héroult process, the dominant industrial method for producing aluminium worldwide. Without these anodes, the electrolysis required to smelt alumina (aluminum oxide) into pure aluminum metal simply cannot occur efficiently.
The primary function of the carbon anode during aluminum electrolysis is twofold. Firstly, it conducts the necessary electric current into the electrolytic bath (molten cryolite containing dissolved alumina). Secondly, and critically, it participates directly in the chemical reaction. The oxygen ions released from the alumina during electrolysis react with the carbon of the anode at high temperature, forming carbon dioxide and carbon monoxide gases. This reaction is why carbon anodes are consumed during the production process. This consumption means anodes need periodic replacement, making them a significant operational cost and a vital consumable in aluminium smelting. Their performance directly impacts energy efficiency, metal purity, and overall production costs.
How is the Carbon Anode Production Process Carried Out?
The carbon anode production is a sophisticated, multi-step process designed to create anodes with specific physical and chemical properties. It begins with the careful selection and preparation of raw materials, primarily petroleum coke and coal tar pitch. The petroleum coke, which acts as the aggregate, is first calcined (heated to high temperature in the absence of air) to remove volatile matter and increase its density and electrical conductivity. This calcined petroleum coke is then crushed and screened into specific size fractions – these are the coke particles.
These sized coke particles are mixed with liquid coal tar pitch, which acts as a binder, holding the coke together. This mixing is done at elevated temperature to ensure the pitch flows and coats the particles effectively. The resulting paste is then formed into large blocks, typically through vibro-compaction or pressing. These "green" anodes are still relatively fragile. The crucial step is baking, where the green anodes are slowly heated in large furnaces over several days to temperatures often exceeding 1100°C. This baking process carbonizes the pitch binder, creating a strong, solid carbon anode block, and drives off any remaining volatile materials. Sometimes, a further treatment process like graphitization (heating to even higher temperatures, ~2500°C+) might be employed for specific applications requiring enhanced properties, though this is less common for standard aluminium smelting anodes compared to, say, graphite electrodes for steel furnaces.
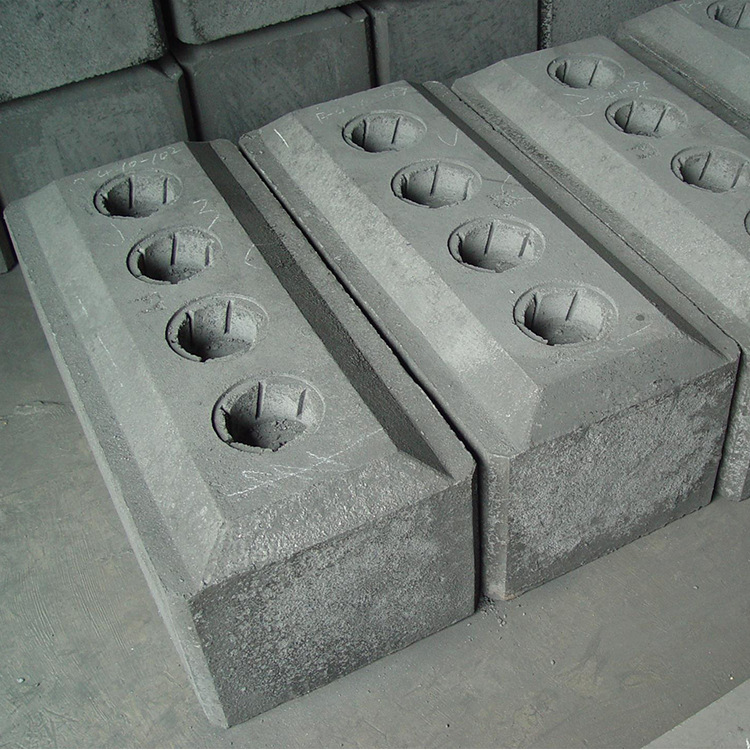
What are the Key Raw Materials, Especially Petroleum Coke, Used in Anode Production?
The quality of the final carbon anode is intrinsically linked to the quality of its input materials. The primary raw material, making up 65-75% of the anode’s mass, is petroleum coke. This is a byproduct of the oil refining process. However, not just any petroleum coke will do. For anode production, low-sulfur, low-metal-content "anode-grade" coke is required. It must undergo calcination, a high-temperature process that significantly alters its structure, improving electrical conductivity and density, which are critical parameters for efficient electrolysis. The consistency and purity of the calcined petroleum coke supply are major focuses for anode manufacturers and, consequently, for aluminium producers. Variations can significantly affect anode performance and consumption rates.
The second key component is the binder, typically coal tar pitch, constituting about 15-25% of the mix. This pitch is derived from the distillation of coal tar, a byproduct of coal coking in the steel industry. The pitch must have specific properties, including appropriate softening point, viscosity, and coking value, to effectively bind the coke particles during mixing and forming, and then to yield a strong carbon matrix after baking. Sometimes, recycled anode butts (the unused portions of spent anodes) are also crushed and added back into the mix, improving resource utilization. Sourcing consistent, high-quality High carbon coal tar asphalt (pitch) and petroleum coke is a constant task for factories like ours, ensuring the final carbon anode meets stringent performance requirements.
The Science Explained: How Do Carbon Anodes Function in Aluminum Electrolysis?
The Hall-Héroult process is the cornerstone of modern aluminum production, and the carbon anode is at its reactive center. The process takes place in large electrolytic cells or "pots." The core of the cell contains a bath of molten cryolite (Na₃AlF₆), typically operating at a temperature around 950-970°C. Alumina (Al₂O₃), extracted from bauxite ore, is dissolved in this molten bath. The carbon anode blocks are suspended in the bath from above, while the cell lining, also made of carbon materials (often graphite blocks), acts as the cathode (negative electrode).
When a powerful electric current (often hundreds of thousands of amperes) is passed through the cell from the carbon anode to the cathode via the molten cryolite electrolyte, the electrolysis process begins. The dissolved alumina dissociates into aluminium and oxygen ions. Positively charged aluminium ions migrate to the cathode, where they gain electrons and deposit as molten aluminum metal (Al³⁺ + 3e⁻ → Al). Simultaneously, negatively charged oxygen ions (O²⁻) migrate to the carbon anode. Here, the electrochemical reaction occurs: the oxygen reacts with the carbon of the anode. This reaction primarily forms carbon dioxide (CO2), although some carbon monoxide is also produced depending on conditions. The simplified overall reaction at the anode is: 2O²⁻ + C → CO2 + 4e⁻. This reaction consumes the carbon anode material, gradually lowering it into the bath over its operational life, which is typically several weeks.
What Role Does Coke Play Beyond Being a Raw Material in Aluminum Smelting?
While petroleum coke is fundamentally the primary raw material for the carbon anode itself, its influence extends beyond simply being the bulk material used. The type and quality of the coke significantly dictate the final properties and performance of the anode within the aluminium smelting cell. The structure formed after calcining and baking impacts critical factors like electrical conductivity, mechanical strength, and reactivity towards oxygen and CO2. High conductivity is essential to minimize energy loss (voltage drop) across the anode, improving the overall energy efficiency of the aluminum production process.
Furthermore, the coke structure influences the anode’s resistance to both mechanical stresses (handling, thermal shock) and chemical attack (oxidation by air and CO2, reaction with cryolite components). A well-structured anode made from high-quality coke will have lower consumption rates, meaning less anode material is needed per tonne of aluminium produced. It will also generate less residue and dusting, contributing to smoother pot operation and reduced friction or operational issues. Therefore, while sometimes viewed as just a fuel source in other industries, in anode production, coke is a highly engineered material whose properties are carefully managed to optimize the entire aluminium electrolysis process. Its quality underpins the efficiency and stability of primary aluminum production.
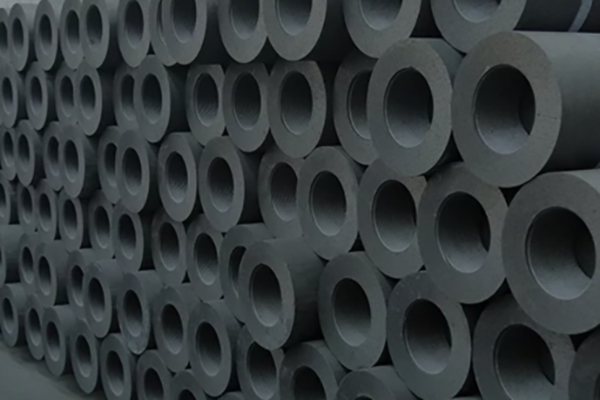
Can You Detail the Technology Behind Aluminum Electrolysis and Anode Consumption?
The core technology for aluminum production remains the Hall-Héroult process, invented independently in 1886. Modern aluminium smelters utilize large, highly controlled electrolytic cells arranged in series ("potlines"). The technology involves passing a very high direct electric current through a series of these cells. Each cell operates at a relatively low voltage (around 4-5 volts) but carries enormous amperage (100,000 to over 500,000 amps). This energy drives the electrolysis process, splitting the strong chemical bonds in alumina.
The consumption of carbon anodes is an inherent part of this technology. As explained, the carbon anode isn’t just a conductor; it’s a reactant. The electrolysis releases oxygen from the dissolved alumina, and this oxygen immediately reacts with the hot carbon surface of the anode. The primary reaction product is carbon dioxide (CO2), essentially burning the carbon anode away using electrochemical energy rather than direct combustion. Theoretically, producing 1 kg of aluminium requires consuming about 0.33 kg of carbon. In practice, due to side reactions (like air burn on the exposed top surface and reaction with CO2 – the Boudouard reaction C + CO2 → 2CO) and some physical wear resistance issues, the actual net consumption is typically higher, around 0.40 to 0.45 kg of carbon anode per kg of aluminium produced. This continuous consumption necessitates the regular replacement of anodes, making anode production capacity a crucial part of any integrated aluminium smelter. The goal of ongoing technological development is to reduce this net consumption rate, improve current efficiency, and lower energy use.
What Makes a High-Quality Anode Material for Aluminum Smelting?
A high-quality carbon anode (anode material) is defined by a set of specific physical and chemical properties crucial for efficient and stable aluminum smelting. Low electrical resistance is paramount; the anode must conduct massive currents with minimal voltage drop to conserve energy. High apparent density is also critical – a denser anode generally means lower porosity, which reduces reactivity to air and CO2, leading to lower consumption rates and longer life. Good mechanical strength and thermal shock resistance are needed to withstand handling, the stresses of insertion into the hot molten cryolite bath, and the operational temperature cycles without cracking or excessive spalling.
Furthermore, purity is essential. Contaminants in the anode material, particularly elements like sulfur, silicon, iron, vanadium, and nickel originating from the petroleum coke or coal tar pitch, can leach into the molten aluminium, affecting its final purity and properties. Low reactivity towards air and CO2 at operating temperatures is also desirable to minimize non-electrochemical consumption. Uniformity is key – consistent properties throughout the anode block and from one anode to the next ensure predictable performance and stable cell operation. Achieving this consistent high-quality requires meticulous control over the raw material selection, the preparation method, and every step of the anode production process. Suppliers like us focus heavily on these quality parameters to meet the demanding needs of the aluminum industry. Our High performance pre baked anode carbon block exemplifies this commitment to quality.
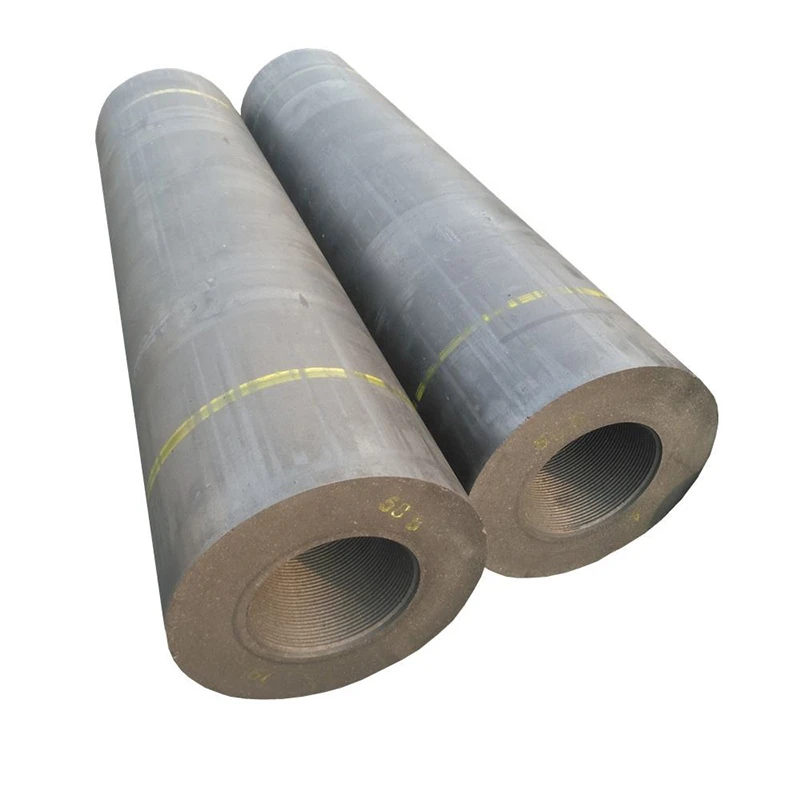
What Are the Major Challenges and Environmental Concerns in Carbon Anode Production and Use?
While essential, the production and use of carbon anodes present significant challenges, particularly concerning environmental impact. The primary concern during aluminium electrolysis is the emission of greenhouse gases (GHG). The direct reaction of the carbon anode with oxygen inherently produces large quantities of carbon dioxide (CO2), a major greenhouse gas. For every tonne of aluminium produced, roughly 1.5 tonnes of CO2 are generated just from anode consumption. Additionally, under certain process upset conditions (low alumina concentration), perfluorocarbons (PFCs), extremely potent GHGs, can be formed. Energy consumption itself, largely generated from fossil fuels in many regions, contributes indirectly to the carbon footprint.
The anode production process also has environmental aspects. Baking furnaces can release pollutants if not properly controlled, including sulfur oxides (from sulfur in the coke), nitrogen oxides, particulate matter, and volatile organic compounds from the pitch binder. Handling petroleum coke and coal tar pitch requires careful management due to potential health and environmental concerns associated with dust and specific chemical compounds like polycyclic aromatic hydrocarbons (PAHs) in pitch fumes. Ensuring consistent raw material quality, managing waste (like spent potlining), and controlling emissions throughout the lifecycle are ongoing challenges for the aluminium industry. The search for materials with better wear resistance and reduced environmental impact continues. Issues like anode cracking or premature failure due to corrosion or mechanical properties also represent operational challenges that impact efficiency and costs.
How Can Technology Mitigate Emissions in the Aluminum Production Process?
The aluminium industry is actively pursuing various technology pathways to mitigate its environmental footprint, particularly GHG emissions. Significant efforts focus on improving the energy efficiency of the Hall-Héroult process itself. Better process control, advanced cell designs, and improved thermal management can significantly reduce the energy needed per tonne of aluminium, thereby lowering indirect emissions if the power source is fossil-fuel based. Optimizing anode quality (like our graphite electrodes made from specific coke) also plays a role, as better conductivity and lower consumption rates contribute to overall efficiency gains. Enhanced monitoring and control systems help prevent anode effects, thus drastically reducing PFC emission incidents. Capturing CO2 from smelter off-gases is being explored, though it presents significant technical and economic challenges.
A major long-term goal is the development of inert anode technology. Unlike carbon anodes that are consumed to produce CO2, inert anodes would ideally conduct electricity and facilitate the release of oxygen as a gas (O2) instead of reacting themselves. Companies like Alcoa (through the Elysis joint venture) are making strides in this area. If successful and commercially viable, inert anodes could fundamentally change aluminum production, eliminating direct CO2 emissions from the electrolysis cell. Other research explores alternative electrolysis processes or novel carbonaceous materials that might offer lower reactivity or enable different chemical pathways. These technological advancements aim to reduce the overall environmental impact and ensure the long-term sustainability of aluminium production. Emissions could potentially be cut dramatically with these future technologies.
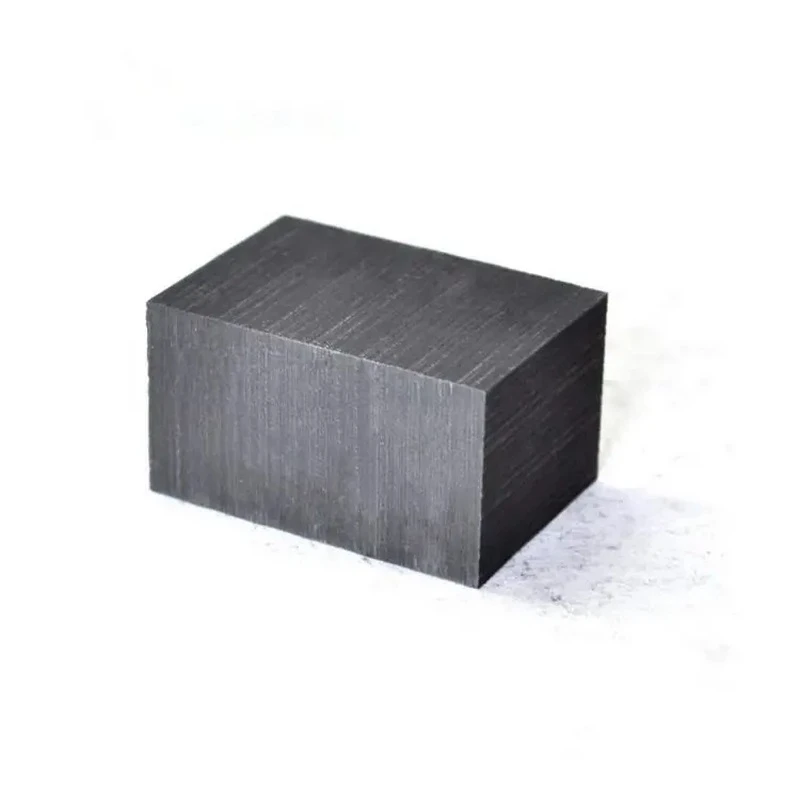
What Should Procurement Professionals Look for When Sourcing Carbon Anodes?
For procurement officers like Mark Thompson, sourcing carbon anodes effectively involves balancing quality, cost, and reliability. Given that anodes are consumed during the electrolysis process, a dependable supply chain is non-negotiable. Beyond competitive pricing, the primary focus should be on consistent quality. This means verifying the supplier’s quality control processes, from raw material inspection (petroleum coke, pitch) to final anode testing. Requesting and verifying certifications (e.g., ISO 9001) and detailed material specification sheets is crucial. Don’t just take certificates at face value; understand the testing methodologies and parameters.
Reliability extends to logistics and communication. Delays in anode shipments can halt production lines, causing significant financial losses. Evaluate the supplier’s track record for on-time delivery and their logistical capabilities, especially for international shipments to regions like the USA or Europe. Clear, efficient communication is also vital. Dealing directly with a knowledgeable representative from the factory, like myself, Allen, from a Professional Graphite Electrode Factory, can streamline discussions and resolve issues faster than going through multiple intermediaries. Technical support, even if the buyer isn’t an engineer, is valuable. A good supplier should be able to discuss anode performance, troubleshoot potential issues related to their product, and explain how their anode material properties (density, conductivity, mechanical strength) align with the buyer’s operational needs. Lastly, ensure transparent and secure payment methods are available. Building a long-term relationship with a reputable manufacturer who understands the demands of the aluminium industry is often the best strategy.
Key Takeaways:
- Carbon anodes are essential consumables in the Hall-Héroult process for aluminium production, acting as conductors and reactants.
- Anode production involves carefully processing petroleum coke and coal tar pitch binder, followed by forming and high-temperature baking.
- The quality of raw materials, especially calcined petroleum coke, directly impacts anode performance (conductivity, density, strength, purity) and consumption rates.
- Carbon anodes are consumed during electrolysis as carbon reacts with oxygen from alumina, primarily forming CO2.
- Key anode quality parameters include low electrical resistance, high density, good mechanical strength, high purity, and low reactivity.
- Major challenges include managing CO2 and other emissions, energy consumption, and ensuring consistent raw material supply.
- Technology advancements focus on improving efficiency, reducing emissions, and developing potentially game-changing inert anodes.
- When sourcing, focus on consistent quality, supplier reliability (logistics, communication), verifiable certifications, technical support, and transparent transactions.
Post time: 04-07-2025