This article provides a deep dive into the world of Ultra-High Power (UHP) graphite electrodes, crucial components in modern steelmaking. We’ll explore their properties, applications, manufacturing processes, and key considerations for procurement. If you’re involved in steel production, electric arc furnace (EAF) operations, or the procurement of graphite products, this article is essential reading, offering insights that can improve your operational efficiency and bottom line. From understanding the different grades to selecting the right supplier, we’ve got you covered.
1. What are UHP Graphite Electrodes and Why are They Important?
UHP (Ultra-High Power) graphite electrodes are essential components in electric arc furnaces (EAFs) used for steelmaking. They conduct the enormous electrical current required to melt scrap metal and refine steel. Their ability to withstand extreme temperatures, high current densities, and aggressive chemical environments makes them indispensable in modern steel production. The primary characteristic of UHP Graphite Electrodes is lower resistivity.
These electrodes are mainly used for ultra-high power electric arc furnace smelting. UHP graphite electrodes are manufactured from high-quality raw materials, primarily petroleum coke and needle coke, undergoing a meticulous process that includes baking, impregnation, and graphitization. This process results in a product with superior thermal and mechanical properties, crucial for efficient and reliable EAF operation. The density and mechanical strength contribute to the long service life.
2. How Does UHP Graphite Electrode Grade Affect Steelmaking Performance?
The grade of a graphite electrode significantly impacts its performance in the EAF. UHP graphite electrodes, representing the highest grade, offer superior electrical conductivity and lower electrical resistance compared to High Power (HP) and Regular Power (RP) electrodes. This translates to greater energy efficiency, reduced electrode consumption, and ultimately, lower production costs.
Choosing the correct grade, like UHP graphite, is critical for maximizing furnace efficiency. A higher grade electrode, while initially more expensive, can lead to significant long-term savings due to its extended lifespan and improved performance in demanding steelmaking environments. The correct selection can also minimize downtime related to electrode breakage or premature wear, thus increasing overall productivity in the steel industry.
3. What are the Key Applications of UHP Graphite Electrodes?
UHP graphite electrodes are widely used in high-power electric arc furnaces (EAFs) for producing high-quality steel and alloy steels. They are also used in ladle furnaces to refine molten steel and adjust its chemical composition. Beyond steelmaking, they find applications in smelting other metals and in the production of nonmetallic materials.
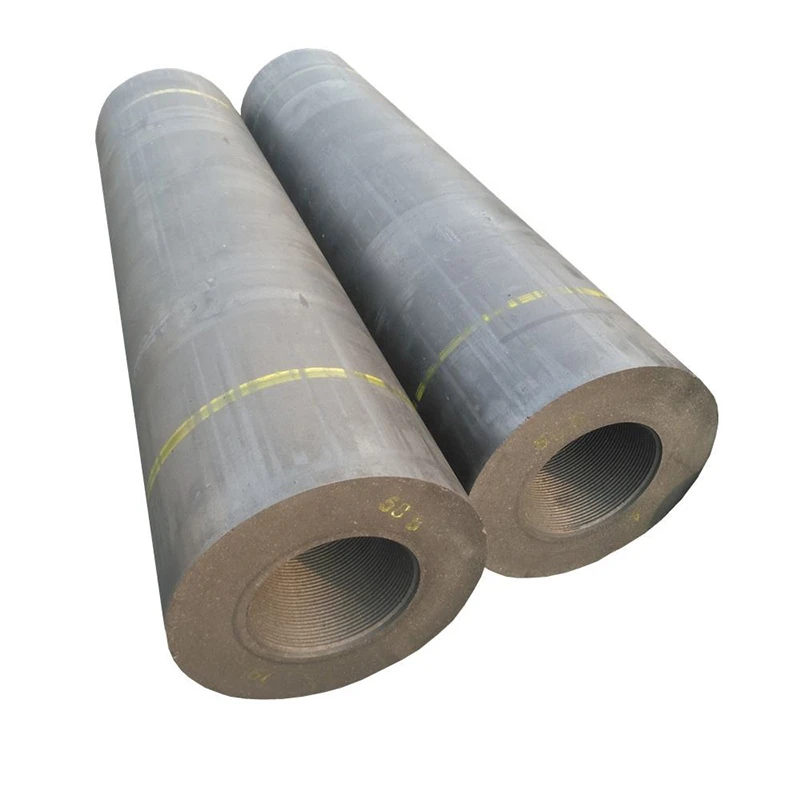
Specifically, UHP graphite electrode application extends to processes requiring extremely high temperatures and precise control, such as the production of alloy steels and specialty metals. Their ability to handle current density greater than 25 A/cm² makes them ideal for these demanding applications.
4. Understanding the Manufacturing Process of UHP Graphite Electrodes.
The manufacturing of UHP graphite electrodes is a complex process involving several key stages. It begins with the careful selection of raw materials, primarily petroleum coke and coal tar pitch. These materials are then mixed, formed into the desired shape, and baked at high temperatures. The product is then graphitized with a nipple.
Following baking, the electrodes undergo impregnation with pitch to improve their density and strength. The final stage is graphitization, where the electrodes are heated to extremely high temperatures (around 3000°C) in a specialized furnace, transforming the amorphous carbon into crystalline graphite. This process imparts the final product with its characteristic low electrical resistance, high thermal conductivity, and excellent oxidation resistance.
5. UHP vs. HP vs. Regular Power Graphite Electrodes: What’s the Difference?
The key difference between UHP, HP, and Regular Power graphite electrodes lies in their electrical resistivity and ability to handle different current densities. UHP electrodes have the lowest resistivity and can withstand the highest current densities, making them suitable for the most demanding EAF operations. HP electrodes offer a balance between performance and cost, while RP electrodes are mainly used for lower-power applications.
Feature | Regular Power (RP) | High Power (HP) | Ultra-High Power (UHP) |
---|---|---|---|
Resistivity (μΩ.m) | > 8.0 | 6.0 – 8.0 | < 6.0 |
Current Density (A/cm²) | < 17 | 17 – 25 | > 25 |
Application | Low-power furnaces | Medium-power furnaces | High-power furnaces |
Density (g/cm³) | 1.55 – 1.65 | 1.60 – 1.70 | 1.65 – 1.80 |
Flexural Strength(MPa) | 8-11 | 9-12 | >12 |
Steel Production Cost | Higher | Medium | Lower |
Choosing between these types depends on the specific requirement of the EAF and the type of steel being produced. UHP graphite electrodes are the preferred choice for high-productivity, high-quality steel production.
6. How to Choose the Right Diameter and Length for Your UHP Graphite Electrodes.
The diameter and length of UHP graphite electrodes are determined by the capacity and design of the electric arc furnace. Common diameters range from 300 mm to 700 mm, with lengths varying depending on the furnace configuration. Correct sizing is crucial for optimal furnace performance and electrode longevity.
Selecting the appropriate diameter is critical for ensuring efficient current transfer and minimizing electrode consumption. For instance, a 700mm electrode is typically used for ultra-high power EAFs with large capacities. The length must be sufficient to reach the molten metal bath while accounting for electrode consumption during operation. An undersized electrode can lead to increased resistance and higher energy consumption, while an oversized electrode may be unnecessarily expensive.
7. What are the Critical Quality Parameters for UHP Graphite Electrodes?
Several quality parameters are critical when evaluating UHP graphite electrodes. These include electrical resistivity, bulk density, flexural strength, and thermal expansion coefficient. These properties directly impact the electrode’s performance, lifespan, and overall cost-effectiveness.
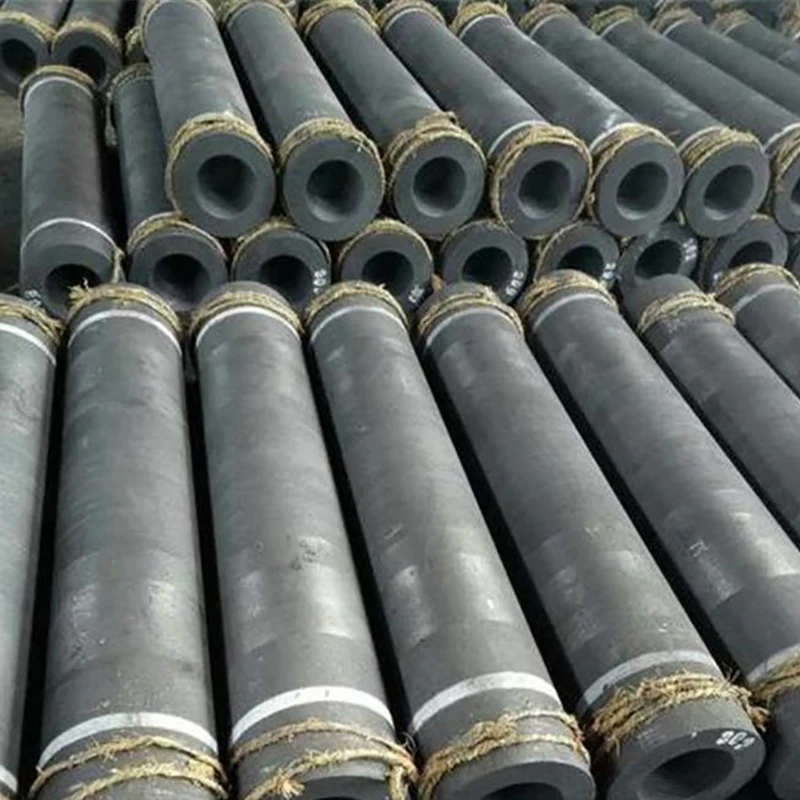
- Electrical Resistivity: Lower resistivity indicates better electrical conductivity, leading to reduced energy loss.
- Bulk Density: High density generally correlates with improved strength and resistance to oxidation.
- Flexural Strength: Higher strength reduces the risk of electrode breakage during operation.
- Thermal Expansion Coefficient: A low coefficient minimizes thermal stress and the risk of cracking under rapid temperature changes. Thermal conductivity must be excellent.
These characteristics are essential to ensure the product quality.
8. How Does China Fare as a Manufacturing Hub for UHP Graphite Electrodes?
China has emerged as a leading manufacturer of UHP graphite electrodes, offering competitive pricing and increasing quality. Numerous Chinese factories, equipped with advanced manufacturing technology, are capable of producing electrodes that meet international standards. However, it’s crucial to carefully vet suppliers to ensure consistent quality and reliability.
While China offers cost advantages, buyers should prioritize quality inspection and due diligence. Requesting certifications (e.g., ISO standards, material specifications) and conducting factory audits can help mitigate risks associated with inconsistent product quality. My name is Allen, and I’m from a China based factory with 7 production lines. We specialize in graphite electrodes. Our product features include low electrical resistance, and excellent oxidation resistance.
9. The Role of Needle Coke in UHP Graphite Electrode Production.
Needle coke, a premium grade of petroleum coke, is the primary raw material used in the production of UHP graphite electrodes. Its unique crystalline structure, characterized by its needle-like shape, contributes to the superior properties of UHP electrodes, including low electrical resistivity and high mechanical strength.
The quality of the needle coke directly impacts the final performance of the graphite electrode. Electrodes made with high-quality needle coke exhibit improved thermal shock resistance, lower consumption rates, and greater durability in demanding EAF environments. Sourcing needle coke from reputable suppliers is therefore a critical step in ensuring the production of high-performance UHP graphite electrodes.
10. Partnering with the Right UHP Graphite Electrode Supplier: Key Considerations.
Choosing the right supplier is paramount when procuring UHP graphite electrodes. Key factors to consider include the supplier’s experience, manufacturing capabilities, quality control processes, and customer service. Requesting detailed product specifications, certifications, and references is essential.
"The steel industry depend on the consistent quality of graphite electrodes. Selecting a reliable supplier is not just about price, it is about ensuring uninterrupted production and maintaining the highest standards of steel quality." – Mark Thompson, Procurement Officer.
Consider the following:
- Experience and Reputation: Look for suppliers with a proven track record in the industry.
- Technical Expertise: Ensure the supplier has a deep understanding of graphite electrode technology and application.
- Quality Assurance: Verify the supplier’s adherence to international quality standards (e.g., ISO 9001).
- Logistics and Support: Assess the supplier’s ability to deliver products on time and provide ongoing technical support.
- Price and Value: Purchase cost-effective graphite electrodes.
Remember to build a strong relationship with your supplier, fostering open communication and collaboration. We also produce High-power graphite electrode, so contact us to learn more. Our Ultra-high power graphite electrode is ideal to smelt scrap steel in an ultra high power electric arc furnace, also our Extra Large Graphite Electrode are available in a variety of sizes to suit your specific needs.
Summary of Key Takeaways
- UHP graphite electrodes are crucial for efficient and cost-effective steel production in electric arc furnaces.
- The grade of the electrode (UHP, HP, RP) significantly impacts performance and consumption rates.
- Needle coke is a critical raw material that determines the quality of UHP electrodes.
- Careful supplier selection is essential, focusing on experience, quality control, and technical expertise.
- Proper sizing (diameter and length) of electrodes is crucial for optimal furnace operation.
- Key quality parameters include electrical resistivity, bulk density, and flexural strength.
- China is a major manufacturing hub for UHP graphite electrodes, but due diligence is vital.
- Understanding the manufacturing process helps in evaluating electrode quality.
- UHP graphite electrodes are also used to refine molten steel in ladle furnaces.
- The right UHP graphite electrode can significantly improve the efficiency of your steelmaking process.
- Consistent and predictable product quality is essential for uninterrupted steel production.
Post time: 03-21-2025