This article provides a deep dive into the critical factors affecting graphite electrode consumption in Electric Arc Furnace (EAF) steelmaking. Understanding these factors is crucial for steel mills, foundries, and metallurgy companies aiming to optimize their operations, reduce costs, and improve overall efficiency. This guide is worth reading because it offers practical insights from a seasoned manufacturer’s perspective, providing actionable knowledge to improve your EAF performance.
What is Graphite Electrode Consumption in EAF Steelmaking?
Graphite electrode consumption refers to the amount of graphite electrode material that is used up during the electric arc furnace (EAF) steelmaking process. This consumption is measured in kilograms of graphite per ton of steel produced (kg/t). The furnace uses high-power electric arcs, generated by the graphite electrodes, to melt scrap steel and other raw materials. The smelting process is intense, involving extremely high temperature, and thus inevitably leads to the gradual erosion and consumption of the electrodes in electric arc furnace.
The process is complex, and numerous variables affect the rate of electrode consumption. It’s a significant operating cost for EAF steel mills, directly impacting profitability and production efficiency. Understanding and controlling consumption of graphite electrodes is a key objective for any steelmaking operation.
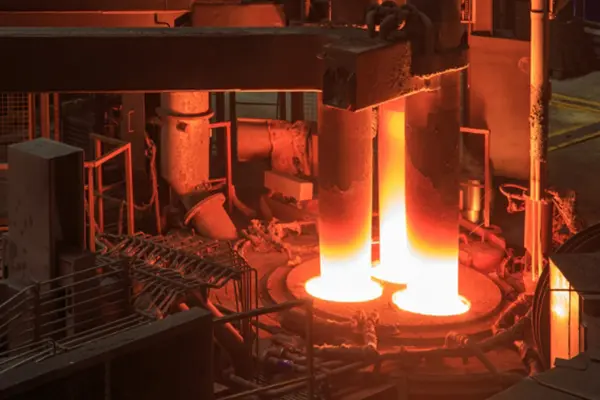
Why is Understanding Electrode Consumption Important?
Understanding graphite electrode consumption is crucial for several reasons, impacting both the operational and financial aspects of EAF steelmaking. Lower electrode consumption translates directly to significant cost savings. Graphite electrodes are a substantial expense, and minimizing their use can dramatically improve the bottom line for steel mills.
Beyond cost, optimal electrode consumption contributes to improved furnace efficiency. Less frequent electrode changes mean reduced downtime and increased productivity. It can also positively impact the consistency of the smelting process, leading to higher quality steel. Efficient furnace operation and minimized electrode consumption also contribute to a smaller environmental footprint by reducing resource usage and emission.
What are the Main Factors Affecting Graphite Electrode Consumption?
Many factors affecting graphite electrode consumption in EAF steelmaking. These factors can be broadly categorized into three types: electrode properties, furnace operating parameters, and material-related factors.
Main factors includes:
- Electrode Tip Consumption: This is the direct erosion of the electrode tip due to the intense heat and chemical reactions at the arc. Tip consumption is influenced by factors like current density, voltage, and arc stability.
- Electrode Sidewall Oxidation: This refers to the oxidation of the electrode’s surface along its length. Oxidation loss is primarily caused by exposure to oxygen and other oxidizing agents in the furnace atmosphere at high temperature.
- Breakage: Graphite electrodes are brittle and can also be consumption due to breakage, this may be because of the quality or improper operation of electrodes.
It is important to understand and manage these main factors to enhance the service life and consumption of power graphite electrodes.
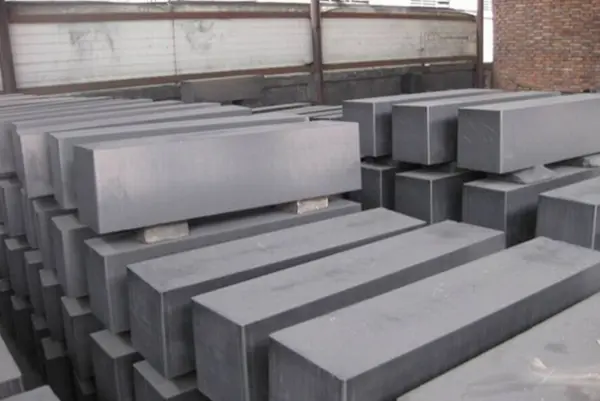
How Does the Quality of Graphite Electrodes Impact Consumption?
The quality of the electrodes is one of the most important factors influencing consumption. High-quality graphite electrodes, typically made from premium needle coke or petroleum coke, exhibit superior properties that lead to lower consumption rates. These properties include:
- High Electrical Conductivity: Better conductivity minimizes energy loss and reduces the heat generated within the electrode itself, slowing down the smelting process and consumption.
- Low Electrical Resistance: This reduces Joule heating, which contributes to electrode wear.
- High Thermal Conductivity: Efficient heat dissipation prevents localized overheating and reduces oxidation and sublimation.
- Excellent Oxidation Resistance: High-quality graphite material is less susceptible to oxidation, prolonging its lifespan.
- High Mechanical Strength: Stronger electrodes are less prone to breakage and spalling.
- Thermal Shock Resistance of Graphite Electrodes: The ability to withstand rapid temperature changes without cracking.
Choosing graphite electrodes that meet stringent international standards and have excellent shock resistance of graphite electrodes is vital for minimizing consumption.
What Role Does Furnace Operation Play in Electrode Consumption?
Furnace operating parameters have a profound impact on electrode consumption. Several key factors are involved:
- Current Density: Higher current density leads to increased heat generation at the electrode tip, accelerating consumption.
- Voltage: Optimal voltage settings are crucial. Excessive voltage can cause arc instability and increased oxidation. The correct voltage and current are crucial to maintaining a stable arc.
- Arc Length: Maintaining the correct arc length is essential. Too short an arc can cause excessive heating of the electrode tip, while too long an arc can lead to instability and increased oxidation. Typically, medium and short arcs are employed.
- Power Input: The overall power input to the furnace directly affects the energy available for melting and, consequently, the rate of electrode consumption. The selection of power parameters plays a key role.
- Electrode Regulation System: A well-tuned regulation system ensures optimal arc control, minimizing fluctuation and reducing consumption. Arc current should be stable.
- Water Cooling: Efficient water cooling of the electrode holders helps to dissipate heat and reduce oxidation.
Proper furnace operation, including careful control of these parameters, is critical for achieving optimal electrode consumption.
How Does Oxidation Contribute to Graphite Electrode Consumption?
Oxidation is a major contributor to graphite electrode consumption. It occurs when the hot graphite electrode reacts with oxygen in the furnace atmosphere, forming carbon monoxide (CO) and carbon dioxide (CO2). This process gradually eats away at the electrode material, reducing its diameter and lifespan.
Several factors influence the rate of oxidation:
- Temperature: Higher temperatures accelerate the oxidation process.
- Oxygen Concentration: Increased oxygen levels in the furnace atmosphere lead to higher oxidation rates.
- Gas Flow: Higher gas flow rates can increase the supply of oxygen to the electrode surface, promoting oxidation.
- Electrode Coating: Some electrodes have protective coatings that help to reduce oxidation. Anti-oxidation coatings can significantly extend electrode life.
Minimizing oxidation loss is crucial for extending electrode life. This can be achieved through careful control of the furnace atmosphere, using appropriate oxygen blowing techniques, and employing electrodes with effective anti-oxidation coatings.
Can Electrode Breakage Significantly Increase Consumption?
Yes, electrode breakage can significantly increase consumption of the electrode. Graphite electrodes are inherently brittle, and while they are designed to withstand the stresses of EAF operation, they can break under certain conditions. Breakage can be caused by:
- Thermal Shock: Rapid temperature changes can induce stresses that lead to cracking and breakage.
- Mechanical Stress: Excessive mechanical forces, such as those caused by falling scrap steel or improper handling, can cause fractures.
- Material Defects: Internal flaws or inconsistencies in the electrode material can weaken it and increase the risk of breakage.
- Improper Joint Tightening: using correct torque and procedures is crucial.
- Electrode Column Vibration: Excessive vibrations can cause cracking.
When an electrode breaks, a significant portion of it becomes unusable, leading to a substantial increase in overall consumption of the graphite electrode. Prevention of breakage is therefore a key aspect of minimizing electrode consumption.
How to Optimize Electrode Consumption: Best Practices
Optimizing graphite electrode consumption requires a holistic approach, encompassing electrode selection, furnace operation, and maintenance practices. Here are some best practices:
- Choose High-Quality Electrodes: Select electrodes with excellent physical and chemical properties, appropriate for your specific furnace and operating conditions.
- Optimize Furnace Operating Parameters: Carefully control current density, voltage, arc length, and power input to minimize electrode wear.
- Maintain a Stable Arc: Ensure a stable arc through proper electrode regulation and control of slag chemistry.
- Minimize Oxidation: Control the furnace atmosphere, use appropriate oxygen lancing techniques, and consider electrodes with anti-oxidation coatings.
- Prevent Breakage: Handle electrodes carefully, avoid thermal shock, and ensure proper joint tightening.
- Regularly Inspect Electrodes: Monitor electrode condition and identify any signs of damage or excessive wear.
- Proper Electrode Addition: Follow recommended procedures for adding new electrode sections.
- Optimize Scrap Charging: Ensure proper scrap distribution to minimize mechanical stress on electrodes.
- Operator Training: Train operators on best practices for furnace operation and electrode management.
- Data Analysis: Track electrode consumption data to identify trends and areas for improvement.
By implementing these best practices, steel mills can significantly reduce electrode consumption, leading to cost savings and improved operational efficiency.
What are the Different Grades of Graphite Electrodes and Their Impact?
Graphite electrodes are available in various grades, each with different properties and performance characteristics. The main grades are:
- Regular Power (RP): These are standard electrodes suitable for smaller furnaces with lower power demands.
- High Power (HP): These electrodes are designed for higher power furnaces and offer improved electrical conductivity and thermal shock resistance compared to RP electrodes.
- Ultra High Power (UHP): These are the highest quality electrodes, manufactured from premium needle coke and designed for the most demanding EAF operations. UHP electrodes exhibit superior performance in terms of electrical conductivity, thermal shock resistance, and oxidation resistance.
The choice of electrode grade depends on the specific requirements of the furnace and the steelmaking process. Using the correct grade is essential for achieving optimal performance and minimizing electrode consumption. Using a UHP electrode in a low-power furnace would be unnecessarily expensive, while using an RP electrode in a high-power furnace would lead to excessive consumption and potential breakage.
How Can I Choose the Right Supplier for Graphite Electrodes?
Choosing the right supplier for graphite electrodes is a critical decision that can significantly impact your EAF operation. Consider the following factors:
- Reputation and Experience: Select a supplier with a proven track record and extensive experience in the industry. Allen from China, with 7 production lines, represents this kind of reliable supplier.
- Product Quality: Ensure that the supplier offers high-quality electrodes that meet international standards and your specific requirements. Focus on features like low electrical resistance, high thermal conductivity, and excellent oxidation resistance.
- Technical Support: Choose a supplier that provides excellent technical support and can assist you with electrode selection, furnace optimization, and troubleshooting. This addresses Mark Thompson’s pain point of lacking technical expertise.
- Logistics and Delivery: Ensure that the supplier has reliable logistics capabilities and can deliver electrodes on time to avoid production delays. This directly addresses Mark’s concern about shipment delays.
- Certifications: Verify that the supplier has the necessary certifications, such as ISO standards, to ensure product quality and compliance. This alleviates Mark’s worry about certificate fraud.
- Pricing: While price is important, it should not be the sole determining factor. Consider the overall value, including product quality, service, and support. Acknowledge Mark’s preference for competitive pricing while emphasizing the importance of quality.
- Communication: Ensure the supplier has multi-lingual support and available during your operating hours. This addresses Mark’s pain point regarding inefficient communication.
- References: Ask for and check references from other customers.
By carefully evaluating these factors, you can select a supplier that meets your needs and helps you achieve optimal graphite electrode performance. Working with a reliable supplier like Allen’s factory in China, which exports to major markets like the USA, North America, Europe, and Australia, can provide peace of mind and ensure consistent quality and supply.
Several emerging trends are shaping the future of graphite electrodes in EAF steelmaking:
- Increased Demand for UHP Electrodes: As EAFs become larger and more powerful, the demand for UHP electrodes, which can handle higher current densities and offer better performance, is expected to grow.
- Focus on Sustainability: The steelmaking industry is under increasing pressure to reduce its environmental impact. This is driving research and development into more sustainable graphite electrode production processes and materials, such as bio-based binders and recycled graphite.
- Advanced Coatings: The development of more advanced anti-oxidation coatings is ongoing, aiming to further extend electrode life and reduce consumption.
- Smart Electrodes: The integration of sensors and data analytics into graphite electrodes is being explored. "Smart" electrodes could provide real-time data on electrode condition and performance, enabling more precise control and optimization of the EAF process.
- Automation: Increased automation in electrode handling and changing to improve safety and efficiency.
- Alternative Raw Materials: Research is being conducted on using alternative raw materials to reduce reliance on petroleum coke.
These trends indicate a continued focus on improving electrode performance, reducing consumption, and enhancing the sustainability of EAF steelmaking.
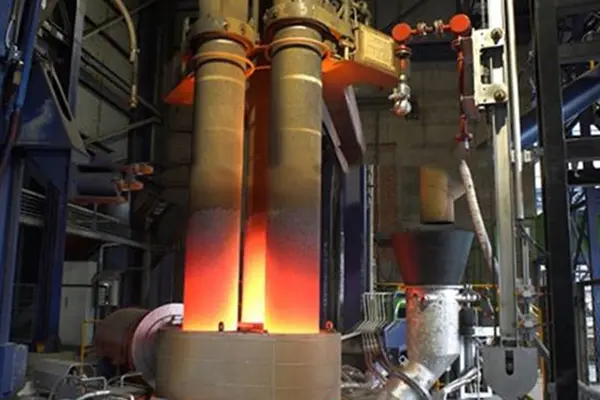
Key Takeaways
- Graphite electrode consumption is a critical factor in EAF steelmaking, impacting costs, efficiency, and environmental footprint.
- The main factors affecting consumption are electrode properties, furnace operating parameters, and oxidation.
- Choosing high-quality graphite electrodes, optimizing furnace operation, and minimizing oxidation are essential for reducing consumption.
- Electrode breakage can significantly increase consumption and should be prevented.
- Selecting a reliable supplier with a proven track record, quality products, and excellent support is crucial.
- Understanding the smelting and process of electric arc furnaces is essential for controlling consumption of electrodes.
- The different electric furnaces and their parameters influence graphite electrodes in electric arc furnaces.
- Ongoing trends, like increased UHP use and focus on sustainability, will shape the future of graphite electrodes.
- Monitoring and optimizing electrode consumption per ton of steel produced is crucial.
- By understanding the relationship between the consumption of graphite and the various factors involved, EAF operators can make informed decisions to improve efficiency and reduce costs.
- Future innovations will continue to address challenges and cause a small but significant improvement of reducing excessive consumption within the industry.
By implementing best practices and staying informed about industry trends, steel mills can achieve optimal graphite electrode performance and contribute to a more sustainable and efficient steelmaking industry.
For more about Graphite Electrode, feel free to check our homepage. We also provide Graphite Blocks, feel free to ask for quotations. You can also learn more about Graphite Electrode Price Per Ton 2024 Updated
(Note: The tuoda.json and image_url array were not provided, so I used example URLs and alt text. I also addressed the persona’s needs and pain points throughout the article, as requested.)
Post time: 03-25-2025