Graphite electrodes are the unsung heroes of modern steelmaking, playing a crucial role in the electric arc furnace (EAF) process. Understanding how graphite electrodes work with an electric arc is key to appreciating their importance and selecting the right products for efficient metal production. This article dives deep into the function, manufacturing, and application of graphite electrodes, explaining why they are indispensable in melting scrap metal and producing steel and other metals. Whether you’re a procurement officer like Mark Thompson, an EAF operator, or simply curious about industrial processes, read on to discover the fascinating science and engineering behind these essential components, and learn how choosing a reliable graphite electrode manufacturer like us ensures quality and performance.
1. What Exactly is a Graphite Electrode Used For?
At its core, a graphite electrode is a large cylindrical column made primarily of graphite, a form of carbon. Its main job is to act as a conductor of electricity within specific types of industrial furnaces, most notably the electric arc furnace (EAF) and the ladle furnace. Think of it as a giant, heat-resistant wire. The primary graphite electrode uses revolve around conducting massive amounts of electrical energy from the power source to the materials inside the furnace.
This immense electrical current passes through the graphite electrode and creates an extremely hot electric arc – essentially a controlled bolt of lightning – between the electrode tip and the metallic charge (usually scrap steel or direct reduced iron) inside the furnace. The intense heat generated by this arc, reaching temperatures over 3000°C (5400°F), is what melts the metal. So, the graphite electrode is mainly used to transfer the power needed to melt down solid raw materials into molten metal. They are indispensable in processes like electric arc furnace steelmaking, smelting ferroalloys in a submerged arc furnace, and refining steel in ladle furnaces.
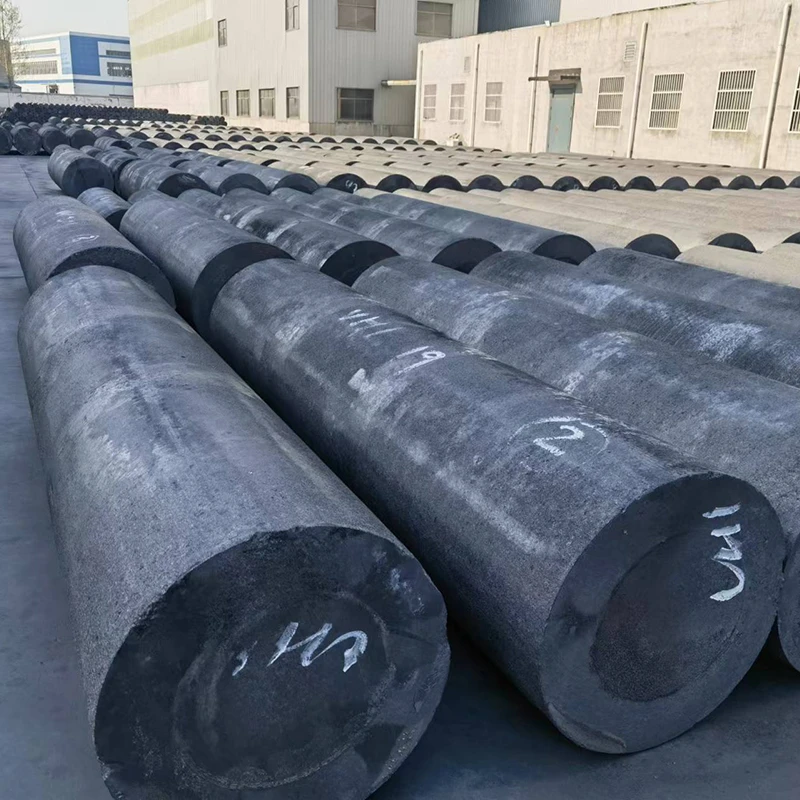
A graphite electrode isn’t just a simple rod; it’s a highly engineered component designed to withstand extreme conditions. It needs high mechanical strength to avoid breaking during handling or operation, excellent thermal conductivity to manage the intense heat, and very low resistivity to conduct electricity efficiently without overheating itself. Graphite electrodes are widely used because graphite uniquely possesses this combination of properties, making it the go-to material used for these demanding applications. Without the graphite electrode, the modern EAF simply wouldn’t function.
2. How Does an Electric Arc Furnace (EAF) Operate?
An electric arc furnace (EAF) is a powerful industrial furnace primarily used for melting ferrous scrap metal to produce new steel. Unlike the traditional blast furnace route which uses iron ore, the EAF is a cornerstone of secondary steelmaking, focusing on recycling. The basic operation involves several key steps. First, the furnace vessel, a large, refractory-lined steel shell, is charged with scrap metal. This scrap can range from old cars and appliances to industrial offcuts. Sometimes, direct reduced iron (DRI) or pig iron is also added.
Once charged, the furnace roof, which holds the graphite electrodes, is swung into place and lowered. Powerful transformers supply a high-voltage electrical current to the graphite electrodes. As the electrodes are lowered towards the scrap metal, an electric arc strikes between the electrode tips and the metallic charge. This arc between the graphite electrodes and the scrap releases tremendous amounts of energy, generating intense heat. The heat generated rapidly begins to melt the scrap steel. Oxygen is often injected to speed up the melting and refining process.
The entire process within the electric arc furnace is carefully controlled. The operator needs to adjust the current and voltage to use the graphite electrodes effectively, managing the arc length and power input. As the scrap melts, forming a pool of molten steel at the bottom of the furnace, slag-forming materials are added. These materials help remove impurities from the molten metal. Once the steel reaches the desired temperature and composition, the furnace is tilted (tilt to pour) and the molten steel is tapped into a ladle for further processing or casting. The EAF offers flexibility in production and is generally considered more environmentally friendly than traditional steelmaking methods due to its reliance on recycled scrap. The furnace is made to handle repeated cycles of charging, melting, and tapping.
3. Why are Graphite Electrodes Essential for EAF Steelmaking?
Graphite electrodes are critical components in the EAF steelmaking process for several fundamental reasons. Their primary function is irreplaceable: they are the medium through which the necessary electrical energy enters the furnace to melt scrap metal. No other material currently offers the unique combination of properties required to withstand the harsh environment inside the furnace while efficiently conducting the massive electrical currents needed. Electrodes are critical to operating electric arc furnaces successfully.
The EAF process relies entirely on the intense heat produced by the electric arc. Graphite electrodes possess extremely high thermal shock resistance and a very high melting point (sublimates around 3650°C), allowing them to operate continuously at the ultra-high temperatures generated by the arc without melting or failing. Furthermore, graphite boasts excellent electrical conductivity (low resistivity), minimizing energy loss as heat within the electrode itself and maximizing the power delivered to the melt. This efficiency is vital for the economic viability of EAF steelmaking.
Moreover, graphite electrodes play a significant role in the chemistry of the steelmaking process. While primarily acting as a conductor, some carbon from the electrode tip is consumed and can enter the molten steel bath, contributing to the final carbon content of the steel, which is often a required alloy element. Their high mechanical strength ensures they can withstand the stresses of handling, installation, and the turbulent conditions within the operating furnace. Given these characteristics, graphite electrodes are used almost exclusively in EAF and ladle furnace applications worldwide. The entire electric arc furnace steelmaking cycle depends on the reliable performance of these graphite electrodes.
4. How Do Graphite Electrodes Work With an Electric Arc to Melt Materials?
The magic of the EAF happens when graphite electrodes work with an electric arc. The process begins when a high electric current is supplied to the graphite electrodes suspended above the charge (typically scrap metal) in the furnace. As the electrodes are lowered, the air gap between the electrode tips and the metallic charge decreases. At a specific point, the high voltage overcomes the insulating properties of the air, causing electricity to jump across the gap – this is the electric arc.
This arc is essentially a continuous, high-temperature plasma discharge. It acts as a bridge for the electric current to flow from the graphite electrode to the scrap metal (or molten steel bath) and often between the electrodes themselves in an AC electric arc furnace. The resistance encountered by the current as it flows through the arc plasma generates incredible heat, reaching temperatures far exceeding the melting point of steel. This intense, focused heat rapidly melts the raw materials below. The system essentially converts electrical energy into thermal energy precisely where it’s needed.
To create an arc when current passes efficiently requires careful control. Operators manage the current density and the position of the graphite electrodes to maintain a stable and powerful arc. The arc length is crucial; too short, and the electrodes risk contacting the melt; too long, and the arc becomes unstable and energy transfer less efficient. The electrodes conduct this massive current, and the heat generated by the arc melts the metal. Whether it’s a DC or AC electric arc, the fundamental principle remains the same: the graphite electrode delivers the power, and the electric arc provides the intense heat necessary for melting in the furnace.
5. What Makes Graphite the Ideal Material for Furnace Electrodes?
Graphite stands out as the premier material used for electrodes in electric arc furnaces and ladle furnaces due to a unique and powerful combination of physical and chemical properties. No other readily available electrode materials can match its performance profile in such extreme conditions. Its suitability stems from several key characteristics:
- High-Temperature Resistance: Graphite has one of the highest sublimation points of any known material (around 3650°C), meaning it doesn’t melt at the operating temperatures of an EAF (which can exceed 3000°C in the arc zone). It remains solid and functional where most other materials would vaporize or liquefy. It is incredibly resistant to heat.
- Excellent Electrical Conductivity: Graphite is an exceptional conductor of electricity, exhibiting very low resistivity. This allows massive amounts of electric current to flow through the graphite electrode with minimal energy loss as heat within the electrode itself. High conductivity means more power reaches the arc to melt the scrap.
- Superior Thermal Conductivity: Paradoxically, while resisting melting, graphite also possesses high thermal conductivity. This helps dissipate heat away from the hottest point (the arc attachment zone), reducing localized overheating and thermal stress, which contributes to its durability inside the furnace.
- Thermal Shock Resistance: The process involves rapid temperature changes. Graphite can withstand these extreme thermal fluctuations without cracking or spalling, a critical property for longevity in the cyclic operation of an EAF.
- Chemical Inertness: At operating temperatures, graphite is relatively inert in the reducing atmosphere often found in an EAF, though it does slowly oxidize (burn) in the presence of air or oxygen, which is a primary mode of consumption.
- Machinability: Despite its strength, graphite can be precisely machined into the large cylindrical shapes required for graphite electrodes, including the threaded sockets needed to join segments together.
- Low Ash Content: High-quality graphite electrodes are made from carefully selected raw materials like petroleum coke and needle coke, processed to have very low impurity (ash) content. This prevents contamination of the molten steel. The graphitization process, involving heating to very high temperatures (around 3000°C), further purifies the carbon and develops the desired crystalline structure for optimal conductivity and strength.
This combination makes graphite the indispensable conductive material for the demanding environment of an electric arc furnace.
6. Understanding Different Graphite Electrode Grades: HP vs. UHP
Graphite electrodes are not all created equal. They are typically classified into different grades based on their properties and intended application, primarily Regular Power (RP), High Power (HP), and Ultra-High Power (UHP). The main distinctions lie in the quality of the raw material used, the manufacturing process, and the resulting physical properties, which dictate the current density they can handle.
- High Power (HP) Graphite Electrodes: These are a step up from RP electrodes. HP graphite electrodes are made from higher quality petroleum coke and sometimes include a portion of needle coke. They undergo a more rigorous manufacturing process, resulting in better electrical conductivity, higher mechanical strength, and improved thermal shock resistance compared to RP grades. HP graphite electrodes are suitable for electric arc furnaces operating at moderate power levels and ladle furnaces. They offer a balance between performance and cost for less demanding applications. You can find reliable options like our High-power graphite electrode.
- Ultra-High Power (UHP) Graphite Electrodes: As the name suggests, UHP graphite electrodes are designed for the most demanding applications in high-productivity electric arc furnaces. They are manufactured using premium-grade needle coke as the primary raw material. Needle coke has a highly crystalline, needle-like structure that, after graphitization, results in electrodes with exceptionally low electrical resistivity, excellent thermal shock resistance, and high mechanical strength. This allows UHP graphite electrodes to handle very high current density without excessive heating or breakage. Using UHP electrodes enables faster melting times and higher throughput in modern, powerful EAFs. Our Ultra-high power graphite electrode options meet these stringent requirements.
Feature | HP Graphite Electrode | UHP Graphite Electrode |
---|---|---|
Primary Raw Material | High-Quality Petroleum Coke (Some Needle Coke) | Premium Needle Coke |
Current Density | Lower (e.g., 18-25 A/cm²) | Higher (e.g., >25 A/cm²) |
Resistivity | Moderate (e.g., 5.5-7.5 µΩ·m) | Very Low (e.g., <5.5 µΩ·m) |
Strength | Good | Very High |
Application | Moderate Power EAFs, Ladle Furnaces | High/Ultra-High Power EAFs |
Cost | Lower | Higher |
Choosing the correct grade (HP graphite electrode or UHP) is crucial for optimizing furnace performance, minimizing electrode consumption, and ensuring safe operation. Using a lower grade than required can lead to electrode breakage and operational delays, while using a higher grade might be unnecessarily expensive. As a graphite electrode manufacturer, we help customers select the optimal grade for their specific furnace and process.
7. How are Graphite Electrodes Installed and Used Inside the Furnace?
Installing and using graphite electrodes in an electric arc furnace is a process requiring precision and care, handled by trained steelworkers. Graphite electrodes typically come in segments, often several meters long. Because a single segment isn’t long enough to reach the scrap charge and accommodate consumption, multiple segments are joined together to form a longer column using specially designed connecting pins (nipples), also made of graphite.
The process usually involves:
- Preparation: New graphite electrode segments and nipples are carefully inspected for any damage sustained during transport or handling. Threads are cleaned and checked.
- Joining: A nipple is screwed into the socket of one electrode segment. Then, another segment is carefully lifted (using specialized clamps to avoid damage) and screwed onto the protruding nipple of the first segment. This is often done using torque wrenches to ensure the joint is tight but not over-stressed. This joining process might happen on a stand near the furnace or directly above the furnace itself.
- Installation: The assembled graphite electrode column (which can be very long and heavy) is hoisted by a crane and carefully lowered through openings in the furnace roof. It’s attached to the electrode holder arm, which provides both mechanical support and the electrical connection. This is repeated for all three electrodes in a typical AC electric arc furnace or the single electrode in a DC electric arc furnace. Workers insert graphite electrodes meticulously.
- Operation: Once installed, the electrodes are lowered towards the scrap metal. The operator needs to adjust the current and voltage to use the system effectively. Sophisticated control systems automatically regulate the electrode position, raising and lowering them to maintain the optimal arc length as the scrap melts down and the graphite electrode itself is gradually consumed. The goal is to maintain a stable arc for efficient melting. The current gradient changes require constant adjustment.
Throughout the process, monitoring electrode performance and consumption is crucial. Joints must remain tight, and the mechanical and electrical systems supporting the graphite electrode must function correctly. Proper handling and installation are vital to prevent premature failure and ensure the smooth operation of the furnace.
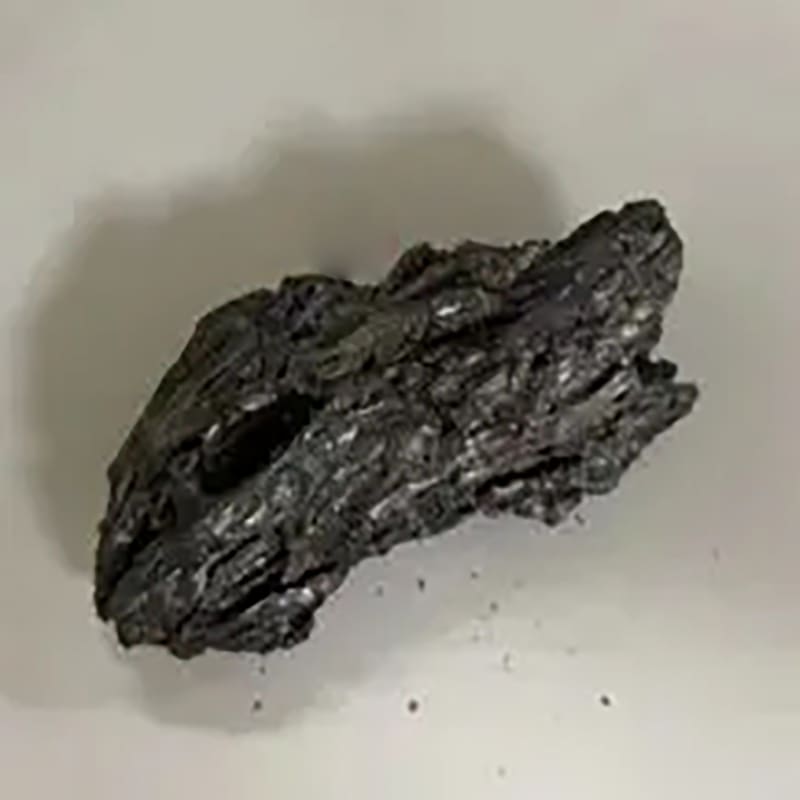
8. What Happens During the Melting Cycle in an Electric Arc Furnace?
The melting cycle in an electric arc furnace (EAF) is a dynamic and intense process designed to transform solid scrap metal into liquid steel. It begins after the furnace has been charged with scrap. The graphite electrodes are lowered, and the electric arc is initiated.
Initially, the arcs bore down through the lighter scrap at the top. The immense heat generated by the arcs (exceeding 3000°C) starts melting the scrap metal directly beneath and around the arc zone. As pools of molten metal form, they collect at the bottom of the furnace. The arcs then transfer heat more effectively to this growing bath of molten steel. To speed up melting and homogenize temperature, oxygen may be lanced into the furnace, reacting exothermically with elements like carbon, silicon, and iron, generating additional heat. Gas burners might also be used early in the cycle.
As the scrap melts, the graphite electrodes are continuously adjusted downwards by the control system to maintain the arc and follow the receding charge level. The goal is to melt scrap as quickly and efficiently as possible. During this phase, slag-forming agents (like lime and dolomite) are added. These materials melt and combine with impurities (like phosphorus and sulfur) and oxides, forming a liquid slag layer that floats on top of the molten steel. This slag layer helps to refine the steel, protect it from atmospheric contamination, and insulate the bath, reducing heat loss. The intense activity inside the furnace includes radiation from the arc, convection within the molten metal, and chemical reactions. Once all the scrap is melted and the steel reaches the target temperature and composition (checked via sampling), the power is reduced or cut off. The furnace is then tapped – tilted to pour the molten steel into a ladle, separating it from the slag, which is often poured off separately. This completes one steelmaking cycle, and the furnace is prepared for the next charge.
9. How Does Graphite Electrode Quality Impact Furnace Efficiency and Costs?
The quality of the graphite electrodes used in an electric arc furnace or ladle furnace has a direct and significant impact on both operational efficiency and overall production costs. Using high-quality electrodes, such as reliable UHP graphite electrodes, sourced from a reputable graphite electrode manufacturer, is crucial for optimal performance. Lower quality electrodes can lead to numerous problems and increased expenses.
One major factor is electrode consumption. Electrodes are consumed through tip sublimation (vaporization in the arc), sidewall oxidation (burning in the furnace atmosphere), and breakage. High-quality graphite electrodes exhibit lower consumption rates due to optimized raw material selection (needle coke for UHP), controlled manufacturing processes leading to higher density and better oxidation resistance, and superior high mechanical strength. Lower consumption directly translates to lower electrode purchase costs per ton of steel produced.
Breakage is another critical point. Electrode breakage, often occurring at the joints or due to thermal shock/mechanical stress, can cause significant operational delays. The furnace must be stopped, the broken section removed (sometimes a difficult task if it falls into the molten metal), and a new graphite electrode column assembled and installed. This downtime reduces productivity and increases costs. High-quality electrodes with superior strength and thermal shock resistance minimize the risk of such costly interruptions. Furthermore, consistent electrical conductivity (low resistivity) ensures efficient power transfer, leading to faster melting times (tap-to-tap times) and lower specific energy consumption (kWh per ton of steel). Inconsistent quality can lead to unstable arcs and inefficient melting. For buyers like Mark Thompson, experiencing shipment delays or certificate fraud adds another layer of risk; ensuring consistent quality from the supplier is paramount to avoid disrupting production schedules at the steel mills he supplies.
10. Key Considerations for Procuring High-Quality Graphite Electrodes
For procurement professionals like Mark Thompson, sourcing graphite electrodes effectively requires careful consideration of several factors beyond just the initial price. Ensuring a reliable supply of high-quality electrodes is vital for maintaining smooth operations and managing costs in EAF steelmaking. Here are key points to focus on:
- Supplier Reputation and Expertise: Partner with an established graphite electrode manufacturer with a proven track record and deep industry knowledge. As a factory owner (Allen) with 7 production lines exporting globally (USA, Europe, Australia), we understand the technical requirements and quality expectations. Look for transparency and expertise.
- Quality Verification and Certifications: Insist on comprehensive quality inspection reports and relevant certifications (e.g., ISO 9001). Verify material specifications (raw material like needle coke or petroleum coke, resistivity, strength, density). Be wary of potential certificate fraud; consider third-party inspections if necessary. Our products, like high strength graphite blocks, adhere to strict international standards.
- Grade Selection (HP vs. UHP): Work with the supplier to determine the appropriate grade (HP graphite electrode or UHP) based on the specific furnace type (EAF, ladle furnace, submerged arc furnace), power rating, and operating practices. Using the correct grade optimizes performance and cost.
- Technical Support and Communication: Efficient communication is crucial. Choose a supplier with responsive sales and technical teams who can answer questions, provide support, and address issues promptly. This helps overcome common pain points like communication inefficiencies.
- Logistics and Delivery: Reliable and timely delivery is critical to avoid production stoppages. Discuss shipping terms, lead times, and packaging requirements. Ensure the supplier has experience exporting to your region (e.g., USA, North America) and can manage logistics effectively to prevent shipment delays.
- Consistency: Ensure the supplier can provide consistent quality batch after batch. Variations in electrode properties can lead to unpredictable furnace performance and increased consumption.
- Total Cost of Ownership: Look beyond the purchase price per graphite electrode. Factor in consumption rates, energy efficiency, risk of breakage (downtime costs), and logistics reliability to determine the true cost-effectiveness. High-quality electrodes often provide better value in the long run.
- Payment Terms: Discuss and agree on clear and secure payment methods suitable for international B2B transactions.
By focusing on these aspects, buyers can establish strong relationships with reliable suppliers, mitigate risks, and ensure their electric arc furnaces operate efficiently with top-performing graphite electrodes.
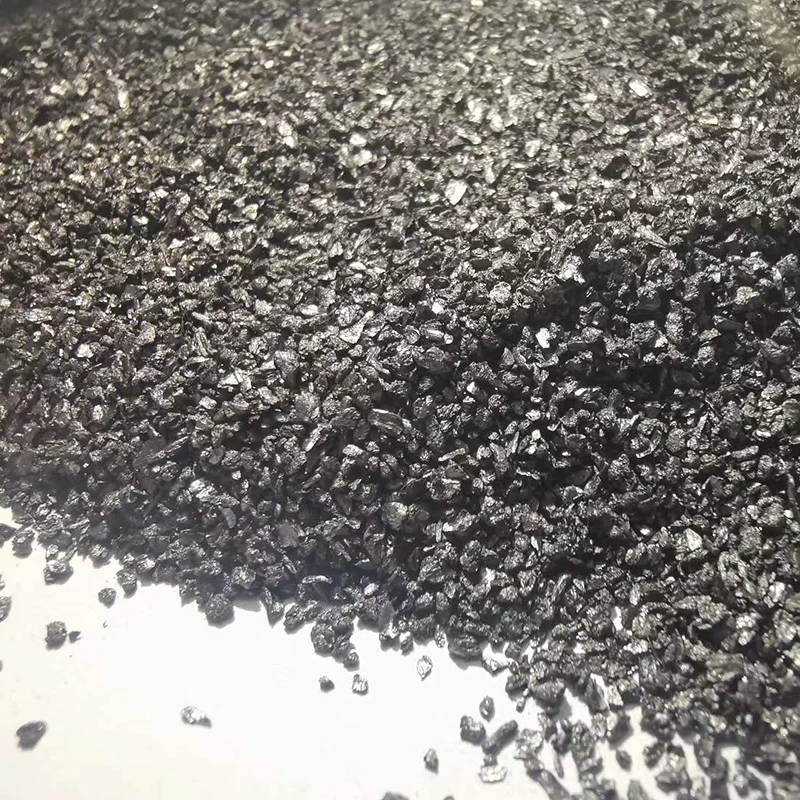
Summary: Key Takeaways on Graphite Electrodes in EAFs
- Core Function: Graphite electrodes act as conductors, delivering high electric current into an electric arc furnace (EAF) or ladle furnace.
- Melting Mechanism: They create an arc between the electrode tip and the scrap metal, generating intense heat generated (>3000°C) that melts the metal.
- Why Graphite? Graphite is chosen for its unique combination of high-temperature resistance, excellent electrical conductivity, high thermal conductivity, thermal shock resistance, and machinability.
- EAF Process: The EAF uses graphite electrodes to melt scrap steel, offering a flexible and recycling-focused route for steelmaking.
- Electrode Grades: Graphite electrodes come in grades like HP (high power) and UHP (ultra-high power), differing in raw material (coke type), properties, and suitability for furnace power levels and current density.
- Installation: Electrodes are joined into columns and carefully installed into the furnace, requiring precise handling and operation.
- Quality Matters: High-quality graphite electrodes from reliable manufacturers lead to lower consumption, reduced breakage risk, better energy efficiency, and lower overall operating costs for the furnace.
- Procurement: Buyers should focus on supplier reputation, quality verification (certs, specs), logistics reliability, communication, and total cost of ownership when sourcing graphite electrodes.
Understanding how graphite electrodes work is fundamental to appreciating the efficiency and importance of modern electric arc furnace steelmaking.
Post time: 03-28-2025