In industries where temperatures soar to unimaginable heights, finding materials that can withstand the heat while providing crucial functions is paramount. This is where high-temperature graphite felt steps into the spotlight. This article dives deep into the world of graphite felt, exploring its unique properties, diverse applications, and why it might just be the carbon and graphite solution you’ve been searching for. If you’re involved in industries like metallurgy, furnace operation, or battery technology, understanding graphite felt is crucial – read on to discover how this advanced material can revolutionize your operations.
1. What Exactly is Graphite Felt and Why is it a High-Temperature Superstar?
Graphite felt is a fascinating material, often unseen but incredibly vital in numerous high-tech and heavy industries. Imagine a soft, flexible fabric, but instead of cotton or wool, it’s made from carbon fibers, processed at extremely high temperatures to become graphite. This transformation gives it remarkable properties, making it a true high-temperature superstar. Its claim to fame is its exceptional thermal insulation capabilities, especially in extreme heat environments. Think about furnaces used in steel mills or specialized equipment in labs – these places need materials that can keep the heat where it should be, and that’s exactly what graphite felt excels at.
But why is graphite felt so good at handling heat? It boils down to its unique structure and composition. The carbon fibers, after being heat-treated, develop a graphitic structure. This structure gives graphite felt a unique combination of properties: it’s lightweight yet strong, flexible yet durable, and most importantly, incredibly resistant to high temperatures. Compared to traditional insulation materials, graphite felt can withstand much higher temperatures without degrading or losing its insulation properties. This makes it indispensable in applications where other materials would simply melt or fail. Plus, the fibrous nature of the felt traps air, further enhancing its thermal insulation capabilities.
2. Rayon Graphite Felt vs. PAN Graphite Felt: What’s the Difference and Which is Right for You?
When you start looking into graphite felt, you’ll quickly encounter two main types: rayon graphite felt and PAN graphite felt. Both are forms of carbon and graphite felt, but they are made from different precursor materials – rayon and polyacrylonitrile (PAN) fibers respectively – and have slightly different characteristics, making them suitable for different applications. So, what’s the real difference, and how do you choose between them?
Rayon graphite felt is derived from rayon, a cellulose-based fiber. When rayon fibers are heat-treated in a process called carbonization and graphitization, they transform into rayon graphite felt. This type of felt is often favored for its high purity and relatively lower cost. It’s known for excellent thermal insulation properties, especially in vacuum environments. On the other hand, PAN graphite felt starts with polyacrylonitrile fibers, a synthetic polymer. PAN-based felt generally boasts higher strength and a higher carbon content after processing. It often exhibits better thermal and electrical conductivity compared to rayon graphite felt.
The choice between rayon graphite felt and PAN graphite felt often depends on the specific application requirements. If high purity and excellent insulation in vacuum are primary concerns, rayon graphite felt is often the go-to choice. It’s commonly used in vacuum furnaces, inert gas furnaces, and for general high temperature insulation in vacuum. If strength, durability, and enhanced thermal conductivity are more critical, PAN graphite felt might be preferred. For instance, in certain battery applications like flow battery systems, or where mechanical stress is a factor, PAN felt could be a better fit. It’s about weighing the pros and cons of each type based on your specific needs.
Here’s a quick comparison table:
Feature | Rayon Graphite Felt | PAN Graphite Felt |
---|---|---|
Precursor | Rayon (Cellulose-based) | Polyacrylonitrile (Synthetic) |
Purity | High | Generally Lower |
Strength | Moderate | Higher |
Thermal Conductivity | Moderate | Higher |
Cost | Generally Lower | Generally Higher |
Best For | Vacuum Insulation, High Purity Needs | Strength, Thermal Conductivity, Durability |
3. How Does Graphite Felt Achieve Such Impressive Thermal Insulation?
The secret behind graphite felt’s impressive thermal insulation lies in its unique fibrous structure and the inherent properties of carbon and graphite. Imagine a dense network of fine carbon fibers, interwoven and layered to create a felt material. This intricate structure is key to trapping heat and preventing its transfer. Think of it like a very effective blanket for high temperatures.
One of the primary reasons for its excellent thermal insulation is the air trapped within the felt structure. Air is a poor conductor of heat, and the numerous tiny air pockets within the graphite felt significantly hinder heat flow. Furthermore, the carbon fibers themselves have a low thermal conductivity, especially in the direction perpendicular to the fiber orientation. This means heat struggles to travel through the fibers and across the felt. The combination of trapped air and low fiber thermal conductivity creates a highly effective thermal insulation barrier.
Moreover, graphite felt is often used in vacuum or inert atmosphere environments, further enhancing its insulation performance. In a vacuum, there’s minimal gas to conduct heat, and graphite felt effectively blocks radiant heat transfer. In inert gas furnaces, the inert atmosphere prevents oxidation of the carbon fibers at high temperatures, allowing the felt to maintain its insulation properties for extended periods. This makes graphite felt an ideal refractory insulation material in demanding high-temperature applications.
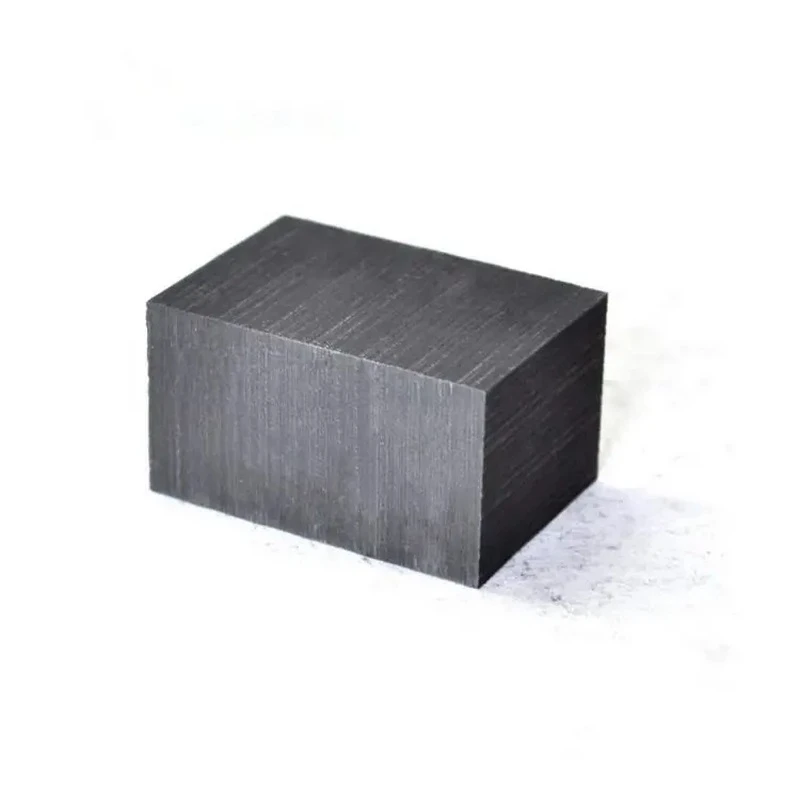
High strength graphite block for various applications.
4. Why is Carbon Content Crucial in High-Temperature Graphite Felt?
The carbon content in graphite felt is a critical factor determining its performance, especially in high-temperature environments. Higher carbon content generally translates to improved thermal stability, enhanced thermal and electrical conductivity, and better resistance to oxidation in inert atmospheres. Think of carbon content as the purity and strength indicator for graphite felt.
During the manufacturing process, precursor fibers (like rayon or PAN) are heat-treated to remove non-carbon elements and promote graphitization. The higher the carbon content, the more complete this graphitization process is, leading to a more structurally sound and thermally robust material. Graphite, being a highly ordered form of carbon, exhibits superior thermal and electrical properties compared to less ordered forms of carbon. Therefore, graphite felt with a higher carbon content will generally perform better in demanding high-temperature applications.
For applications requiring extreme thermal stability and performance in vacuum furnaces or inert gas furnaces, opting for graphite felt with a higher carbon content is often beneficial. It ensures the material can withstand prolonged exposure to high temperatures without significant degradation or loss of its thermal insulation or other desired properties. While higher carbon content often comes with a slightly higher cost, the improved performance and longevity can justify the investment, especially in critical industrial processes. For instance, in vacuum metallurgy processes, maintaining consistent temperature and atmosphere is vital, and high carbon content graphite felt contributes significantly to achieving this.
5. Graphite Felt in Vacuum Furnaces and Inert Gas Furnaces: A Match Made in High-Temperature Heaven?
Graphite felt and vacuum furnaces and inert gas furnaces are indeed a perfect match, forming a cornerstone of many high-temperature industrial processes. The unique properties of graphite felt, particularly its excellent thermal insulation in vacuum and inert atmospheres and resistance to extreme temperatures, make it an indispensable component in these types of furnaces. Imagine trying to operate a vacuum furnace without effective insulation – it would be incredibly energy-inefficient and difficult to maintain the required temperature.
In vacuum furnaces, the absence of air eliminates heat transfer through convection and conduction via gases. Radiant heat transfer becomes dominant. Graphite felt, with its low thermal conductivity and ability to absorb and scatter radiant heat, acts as a highly effective thermal insulation. It minimizes heat loss from the hot zone, allowing the furnace to reach and maintain high temperatures with less energy input. Similarly, in inert gas furnaces, where an inert gas like argon or nitrogen is used to prevent oxidation, graphite felt provides crucial thermal insulation while also being compatible with the inert atmosphere. The inert gas further enhances the lifespan of the graphite felt by preventing it from oxidizing at high temperatures.
The use of graphite felt in vacuum furnaces and inert gas furnaces is widespread across various industries, including metallurgy, ceramaterials processing, and advanced materials manufacturing. From heat-treating aerospace components in vacuum furnaces to sintering ceramics in inert gas furnaces, graphite felt ensures efficient and reliable high-temperature processing. Its ability to withstand extreme temperatures in these controlled atmospheres makes it a truly invaluable material for these demanding applications. The combination of graphite felt and controlled atmosphere furnaces enables precise temperature control and energy efficiency, which are critical for producing high-quality materials and components.
6. What Makes Graphite Felt an Ideal Material for Thermal Conductivity Applications?
While graphite felt is primarily known for its thermal insulation, it also exhibits interesting thermal conductivity properties that are valuable in specific applications. Although its thermal conductivity is lower than solid graphite, it is still significantly higher than many other insulation materials, especially in certain directions. This unique characteristic makes it useful in situations where both thermal insulation and controlled heat dissipation are required.
The thermal conductivity of graphite felt is anisotropic, meaning it varies depending on the direction of heat flow. Heat conduction is more efficient along the plane of the felt layers than through the thickness. This directional thermal conductivity can be advantageous in applications where heat needs to be spread out or channeled in a specific direction while still providing overall thermal insulation. For example, in some battery designs or heat exchangers, graphite felt can be used to conduct heat away from critical components while simultaneously insulating the surrounding areas.
Furthermore, the thermal conductivity of graphite felt can be tailored to some extent by adjusting the fiber orientation, density, and processing parameters during manufacturing. This allows engineers to fine-tune the thermal performance of graphite felt for specific application needs. While not as highly conductive as solid graphite electrode materials, graphite felt’s combination of moderate thermal conductivity and excellent thermal insulation opens up unique possibilities in thermal management and heat transfer applications, particularly in high-temperature and controlled atmosphere environments. Its flexibility and conformability also allow it to be used in complex shapes and spaces where solid graphite might be impractical.
7. Beyond Furnaces: Exploring the Diverse Applications of Graphite Felt in Metallurgy and Beyond.
While vacuum furnaces and inert gas furnaces are major applications, the versatility of graphite felt extends far beyond just furnaces. Its unique combination of properties makes it valuable in a wide range of industries, including metallurgy, energy storage, chemical processing, and even aerospace. Let’s explore some of these diverse applications.
In metallurgy, besides furnace insulation, graphite felt is used in processes like aluminum casting and precious metal refining. Its high-temperature resistance and inert nature make it suitable for handling molten metals and preventing contamination. In energy storage, particularly in advanced battery technologies like redox flow battery systems, graphite felt serves as an electrode material. Its conductive nature, high surface area, and porosity are crucial for efficient energy storage and conversion in flow batteries.
Beyond these, graphite felt finds applications in thermal insulation for high-temperature pipelines, as a component in fuel cells, and as refractory insulation in various industrial heating systems. Its flexibility and easy to cut nature allow it to be easily shaped and customized for different applications. In research and development, graphite felt is used in experimental setups requiring high temperature insulation in vacuum or inert atmosphere. Its lightweight nature and excellent thermal performance make it ideal for creating efficient and compact thermal systems. The ongoing development of advanced materials and technologies continues to uncover new and innovative uses for graphite felt, solidifying its position as a crucial material in numerous industries.
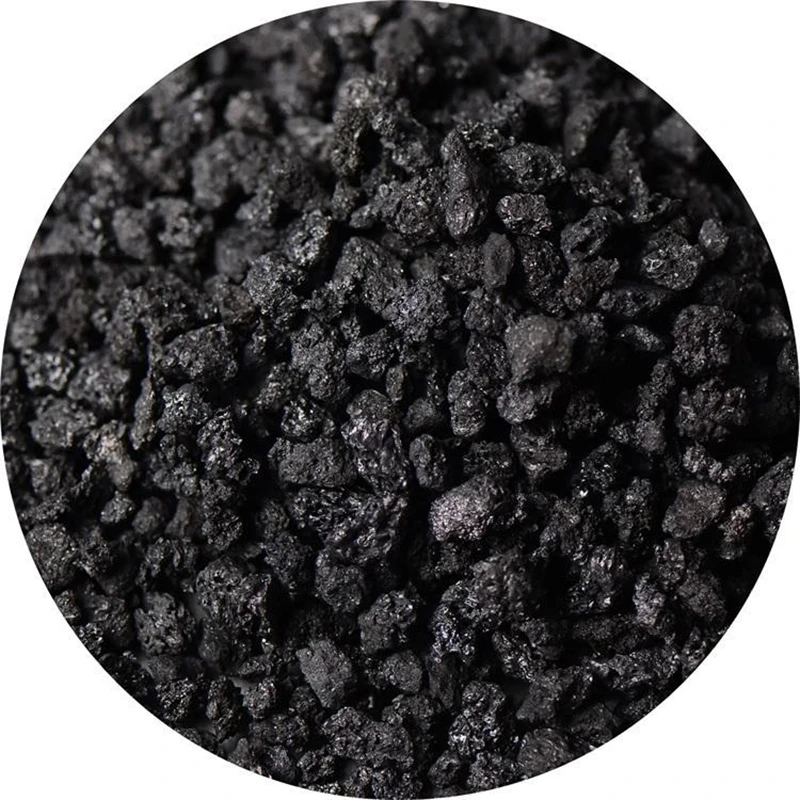
High purity graphite powder for various industrial uses.
8. Considering Rayon Felt for Your Needs? Understanding its Unique Properties and Benefits.
Rayon felt, specifically rayon graphite felt, holds a special place within the graphite felt family due to its unique properties derived from its rayon based precursor. Understanding these properties is crucial when considering rayon felt for specific applications. One of the key advantages of rayon graphite felt is its high purity. The rayon precursor, after purification and processing, results in a graphite felt with very low ash content and minimal impurities. This high purity is particularly important in applications where contamination is a concern, such as in semiconductor processing or certain types of metallurgy.
Another significant benefit of rayon graphite felt is its excellent thermal insulation in vacuum. It performs exceptionally well as insulation in vacuum furnaces and other vacuum environments. The thermal conductivity of rayon graphite felt is typically lower than PAN graphite felt, making it a more effective thermal insulator, especially at very high temperatures in vacuum. This is why rayon graphite felt is often the preferred choice for vacuum furnace linings and high temperature insulation in vacuum.
However, rayon graphite felt generally has lower mechanical strength and lower surface area and better oxidation resistance compared to PAN felt. It is also more susceptible to oxidize in air at high temperatures if not properly protected by an inert atmosphere or vacuum. Therefore, rayon graphite felt is best suited for applications where high purity, excellent insulation in vacuum, and moderate mechanical demands are the primary requirements, such as vacuum furnaces, inert gas furnaces, and certain types of heat-treat processes conducted in controlled atmospheres.
9. How Does the Thickness of Graphite Felt Impact its Performance?
The thickness of graphite felt is a crucial parameter that directly affects its thermal insulation performance and overall suitability for various applications. Generally, thicker graphite felt provides better thermal insulation, but it can also impact other factors like flexibility and space requirements. Think of thickness as directly proportional to the level of thermal insulation you can achieve.
A thicker layer of graphite felt means a longer path for heat to travel through, resulting in reduced heat transfer. This is because thermal insulation is directly related to the material’s thickness and inversely related to its thermal conductivity. Therefore, to achieve higher levels of thermal insulation, especially at very high temperatures, using thicker graphite felt is often necessary. For example, in large vacuum furnaces operating at extremely high temperatures (e.g., 3000℃ or 5432℉), thick layers of graphite felt are essential to minimize heat loss and maintain energy efficiency.
However, increasing the thickness also has some trade-offs. Thicker felt can be less flexible and may not conform as easily to complex shapes. It also occupies more space, which can be a concern in compact equipment designs. Furthermore, excessively thick felt might not always be necessary, especially at lower temperatures or in applications where space is limited. Therefore, selecting the appropriate thickness of graphite felt involves balancing the required thermal insulation performance with factors like space constraints, flexibility needs, and cost considerations. It’s about finding the optimal thickness that provides the desired level of thermal insulation without compromising other critical aspects of the application.
10. Looking for High Purity Graphite Felt? What to Consider for Demanding Applications.
For demanding applications, especially in industries like semiconductor manufacturing, nuclear energy, and advanced ceramaterials processing, high purity graphite felt is often a must. Purity in graphite felt refers to the absence of trace impurities, such as ash, metals, and other non-carbon elements. These impurities can negatively impact performance, especially at high temperatures or in sensitive environments. When seeking high purity graphite felt, several factors need careful consideration.
Firstly, the precursor material plays a crucial role. Rayon graphite felt is inherently higher purity than PAN graphite felt due to the nature of the rayon precursor. Therefore, for ultra-high purity needs, rayon based graphite felt is often the preferred choice. Secondly, the manufacturing process is critical. Stringent purification steps, such as high temperature gas purification and acid leaching, are employed to remove impurities and achieve the desired purity levels. Reputable manufacturers of high purity graphite felt will typically provide detailed specifications on purity, including ash content and trace element analysis.
Thirdly, consider the specific application requirements. The level of purity needed will depend on the sensitivity of the process. For instance, applications in nuclear reactors or semiconductor wafer fabrication demand extremely high purity to prevent contamination and ensure reliable operation. Finally, be prepared for a potentially higher cost for high purity graphite felt. The additional purification steps and quality control measures increase the production cost. However, for critical applications where purity is paramount, the investment in high purity graphite felt is often essential to ensure performance and prevent costly failures or contamination issues. Always request and review the manufacturer’s purity data sheets and certifications to verify the felt meets your specific purity requirements.
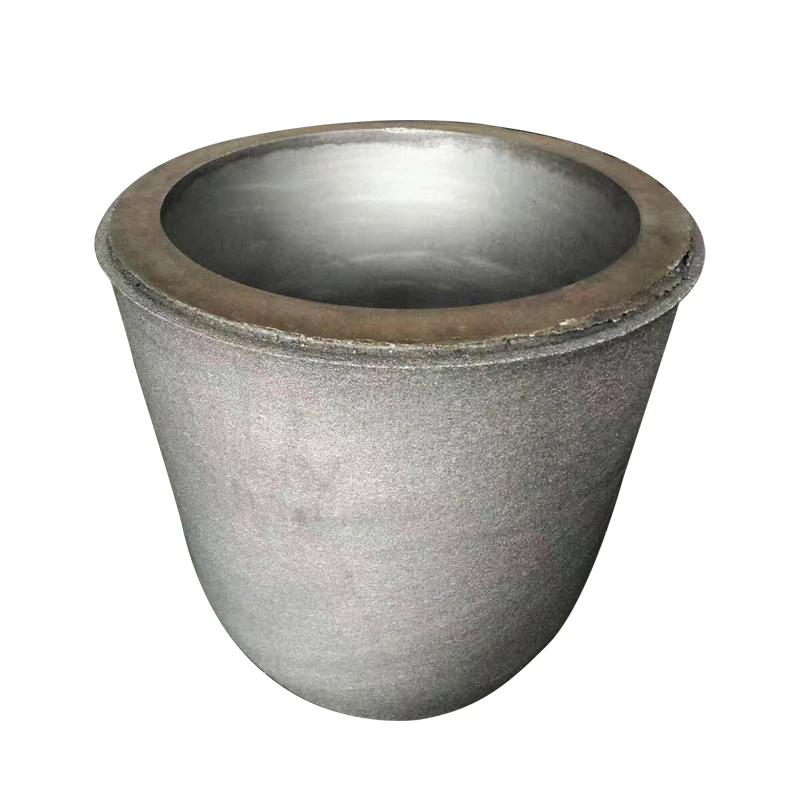
High temperature resistant graphite crucible for melting.
11. Graphite Felt: An Easy-to-Cut Material for Customized Thermal Solutions?
Yes, graphite felt is indeed known for being an easy to cut material, which is a significant advantage when it comes to creating customized thermal solutions. Its fibrous and relatively soft nature allows it to be easily cut, shaped, and formed using standard cutting tools like scissors, knives, or die-cutting equipment. This easy to cut characteristic is particularly beneficial for prototyping, custom installations, and applications requiring complex or non-standard shapes of thermal insulation.
Imagine you need to insulate a piece of equipment with irregular contours or fit insulation into a tight space. With graphite felt, you can readily cut it to the exact dimensions and shape needed, minimizing waste and ensuring a precise fit. This is in contrast to rigid insulation materials that may require specialized cutting tools or be difficult to shape accurately. The easy to cut nature of graphite felt also simplifies installation and maintenance. It can be quickly trimmed and adjusted on-site, saving time and labor.
Furthermore, the flexibility of graphite felt complements its easy to cut property. It can be easily wrapped around curved surfaces, folded into corners, and compressed into gaps, providing thermal insulation even in challenging geometries. This combination of easy to cut and flexible characteristics makes graphite felt a highly versatile material for creating customized thermal solutions in a wide range of applications, from laboratory equipment to industrial furnaces and beyond. Whether you need simple shapes or intricate designs, graphite felt offers the ease of fabrication needed for tailored thermal insulation solutions.
Key Takeaways: Graphite Felt Essentials
- High-Temperature Hero: Graphite felt excels in extreme heat environments, providing crucial thermal insulation up to 3000°C (5432℉) in vacuum or inert atmosphere.
- Rayon vs. PAN: Rayon graphite felt offers higher purity and better insulation in vacuum, while PAN graphite felt provides higher strength and thermal conductivity.
- Insulation Mechanism: Its fibrous structure traps air and minimizes heat transfer, making it a superior thermal insulator.
- Carbon Content Matters: Higher carbon content enhances thermal stability and performance, especially in demanding applications.
- Furnace Favorite: Graphite felt is indispensable in vacuum furnaces and inert gas furnaces, ensuring energy efficiency and precise temperature control.
- Beyond Insulation: While primarily an insulator, it also offers tailored thermal conductivity for specific heat management needs.
- Diverse Applications: From metallurgy and battery technology to aerospace, its versatility is unmatched.
- Rayon’s Purity Advantage: Rayon graphite felt is ideal when high purity is critical, minimizing contamination risks.
- Thickness for Insulation: Thicker felt generally means better thermal insulation, but consider space and flexibility needs.
- High Purity Demands: For sensitive applications, choose high purity graphite felt, especially rayon based, and verify manufacturer certifications.
- Easy Customization: Graphite felt is easy to cut and shape, enabling tailored thermal solutions for various equipment and geometries.
For additional information or to discuss your specific graphite felt needs, please contact us today. We are a professional graphite electrode factory with 7 production lines, ready to supply high-quality graphite materials to meet your requirements. Explore our range of graphite products, including high strength graphite block, high-power graphite electrode, and high temperature resistant graphite crucible. We export to the USA, North America, Europe, and Australia, serving steel mills, foundries, and metallurgy companies with precision-machined graphite solutions.
Post time: 01-24-2025