Choosing the right electrode material for Electrical Discharge Machining (EDM) is a critical decision that directly impacts efficiency, cost, and the final quality of your machined parts. For years, copper electrodes were the standard, but graphite electrodes have gained significant popularity, offering distinct advantages in many EDM applications. If you’re like Mark Thompson, a savvy procurement officer or business owner in the USA, constantly evaluating options from suppliers in China or Vietnam, you understand the importance of balancing quality and cost. This article dives deep into the graphite or copper debate, exploring the advantages and disadvantages of each, helping you decide which electrode to choose – graphite or copper – for your specific EDM machining needs. We’ll cover everything from machinability and wear rates to surface finish and overall cost-effectiveness, drawing on my experience, Allen, as a factory owner producing graphite electrodes and graphite products in China for clients worldwide.
What Exactly is EDM Machining and Why is the Electrode Material So Critical?
Electrical Discharge Machining, or EDM, is a non-traditional manufacturing process. Think of it like controlled erosion using electricity. Instead of cutting material away with a sharp tool, EDM uses electrical sparks (discharges) jumping between an electrode and the workpiece, both submerged in a dielectric fluid. Each spark melts and vaporizes a tiny amount of material from the workpiece, gradually creating the desired shape. The electrode acts as the "tool," and its shape is mirrored onto the workpiece. This process is fantastic for creating complex shapes and forms or machining very hard materials that are difficult or impossible to handle with traditional methods. You can cut out complex shapes with incredible precision.
The choice of electrode material is absolutely fundamental in EDM machining. Why? Because the electrode itself is subject to wear during the process. The properties of the electrode material – its electrical conductivity, thermal conductivity, melting point, and resistance to wear – directly influence several key factors:
- Machining Speed (Material Removal Rate – MRR): How quickly material is removed from the workpiece.
- Electrode Wear (EW): How much of the electrode material is consumed during the process. Lower wear means the electrode maintains its shape longer, improving accuracy and reducing the need for multiple electrodes.
- Surface Finish: The quality and texture of the final surface on the workpiece.
- Overall Cost: Including material cost, machining time for the electrode itself, and the number of electrodes needed per job.
Therefore, selecting the right electrode material – typically deciding between graphite or copper – is not just a technical detail; it’s a strategic decision impacting productivity, precision, and profitability for businesses performing EDM. The electrode must be able to withstand the intense heat and electrical discharges inherent in the EDM process while efficiently transferring the current from the electrode to the workpiece.
Understanding Graphite Electrodes: What Makes Them Tick in EDM?
Graphite electrodes are a popular choice in modern EDM applications. What is graphite? Graphite is a mineral, a form of carbon. Unlike diamond (another form of carbon), graphite is a non-metal that exhibits excellent electrical conductivity, making it suitable for use as an electrode. Graphite electrodes are made from a mixture of petroleum coke (often high-quality needle coke for premium grades like our Ultra-high power graphite electrode specific calcined needle coke block), pitch binder, and other additives. This mixture is extruded or molded, baked, and then graphitized at extremely high temperatures (up to 3000°C). This process aligns the carbon crystals, giving graphite its unique properties.
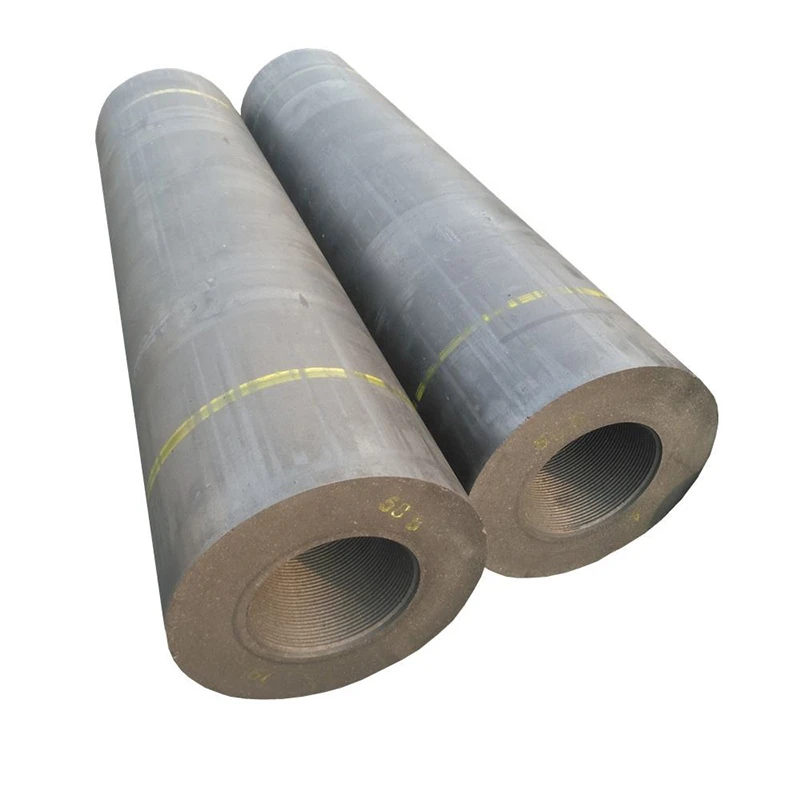
The key properties that make graphite electrodes effective for EDM include:
- High Thermal Resistance: Graphite has an incredibly high melting point (sublimes around 3650°C), allowing it to withstand the intense heat generated during EDM without melting easily.
- Good Electrical Conductivity: While not as high as copper, graphite’s conductivity is sufficient for efficient sparking in EDM. Different grades offer varying conductivity levels.
- Excellent Machinability: Graphite material is relatively easy to machine into intricate shapes, which is a significant advantage when creating complex EDM tooling. Machining graphite can be done quickly and precisely on standard milling machines (often requiring dust collection systems).
- Low Wear Rate: Under optimal conditions, graphite electrodes exhibit lower wear rates compared to copper, especially in roughing operations. This results in less wear and better form-holding.
- Lightweight: Graphite is made of carbon and is much lighter than copper. A piece of copper weighs significantly more than a piece of graphite the same size. This reduces stress on the EDM machine‘s servo mechanisms, especially with large electrodes.
As a factory, we produce various grades, from Regular Power Graphite Electorode suitable for less demanding tasks to High-power graphite electrode and Ultra-high power graphite electrode grades designed for maximum efficiency and minimal wear in high-performance EDM and electric arc furnace applications. The better the graphite quality (finer grain size, higher density), the better the performance in terms of wear and achievable surface finish.
Copper Electrodes Explained: The Traditional Choice for EDM?
Copper electrodes have been a mainstay in EDM machining for decades and are still widely used. Copper is a metallic element known for its outstanding electrical conductivity, which is its primary advantage as an electrode material. Electrodes made of copper allow for efficient transfer of electrical energy to the workpiece. Typically, electrolytic copper or tellurium copper alloys are used for EDM electrodes. Copper electrode materials are dense and offer good wear resistance in certain applications, particularly finishing.
Why were copper electrodes the traditional go-to?
- Superior Electrical Conductivity: Copper’s primary strength. It allows high currents to flow with minimal resistance, which was crucial in older EDM machine designs.
- Good Surface Finish: Copper electrodes are often associated with achieving very fine surface finishes, particularly in finishing passes with positive polarity.
- Familiarity: Being the established material, many shops have extensive experience and optimized parameters for using use copper electrodes.
- Strength: Copper alloys are generally tougher and less brittle than graphite, reducing the risk of chipping or breakage during handling or setup, especially for very fine details.
However, copper also comes with drawbacks. Its lower melting point compared to graphite makes it more susceptible to wear, especially at higher amperages used in roughing operations. Copper is more difficult and slower to machine than graphite, requiring specific tooling and potentially leading to higher electrode fabrication costs. Furthermore, the "stickiness" of copper during machining can be a challenge. While copper is a better conductor, the practical implications in modern EDM machines with sophisticated power supplies often mean that the theoretical conductivity advantage doesn’t always translate into significantly faster overall machining times when electrode wear and machinability are factored in.
Graphite vs Copper: How Do They Stack Up in Key Performance Metrics?
When choosing between graphite and copper electrodes for EDM, a direct comparison of key performance metrics is essential. Here’s a table summarizing the main differences:
Feature | Graphite Electrode | Copper Electrode | Notes |
---|---|---|---|
Machinability | Excellent (3-5 times faster than copper) | Fair to Good (Slower, can be "sticky") | Graphite allows for easier creation of complex shapes. |
Wear Resistance | Generally Better (especially roughing) | Good (can excel in fine finishing) | Graphite typically requires fewer electrodes for a job. |
Material Removal Rate (MRR) | Generally Higher | Can be high, but often limited by wear | Modern machines often achieve higher MRR with graphite. |
Electrical Conductivity | Good to Very Good | Excellent | Copper’s advantage is less pronounced with modern power supplies. |
Thermal Conductivity | Good | Very Good | Graphite’s high melting point compensates for lower thermal conductivity. |
Melting Point | Very High (Sublimes ~3650°C) | Relatively Low (~1085°C) | Graphite withstands higher temperatures and amperages better. |
Surface Finish | Good to Excellent (depends on grade) | Very Good to Excellent | Copper sometimes preferred for mirror finishes. |
Material Cost | Variable (can be higher for premium grades) | Generally Lower (raw material) | Overall cost depends heavily on machining and usage. |
Weight | Lightweight | Heavy | Lighter graphite reduces machine stress. |
Brittleness | More Brittle | Tougher | Copper is less prone to chipping delicate features during handling. |
This table highlights the trade-offs. While copper electrodes boast superior electrical conductivity, graphite electrodes often win in machinability, wear resistance, and overall speed, especially with modern EDM machine technology. The graphite vs copper decision isn’t always clear-cut and depends heavily on the specific EDM task.
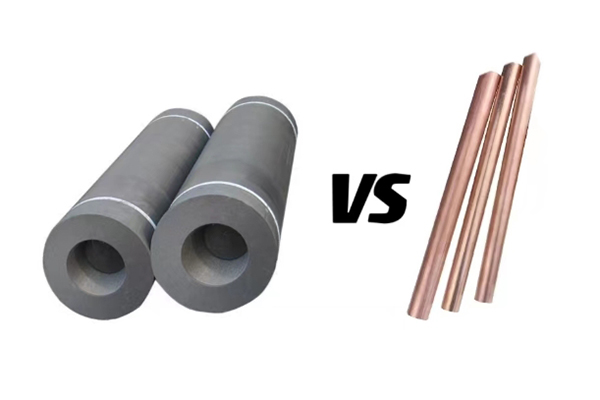
Is Machining Graphite Easier or Harder Than Copper for EDM Electrodes?
From a pure machining perspective, graphite material is significantly easier and faster to machine than copper. As mentioned, machining graphite can be three times faster than copper, sometimes even up to five times faster. Graphite cuts freely, produces small chips (dust), and doesn’t have the "gummy" or "sticky" tendency that can make copper challenging. This allows for higher cutting speeds and feed rates, drastically reducing the time required to fabricate the electrode. Complex geometries, sharp corners, and fine details can be milled into graphite electrodes with relative ease using standard CNC milling machines (though dust extraction is crucial for health and machine longevity).
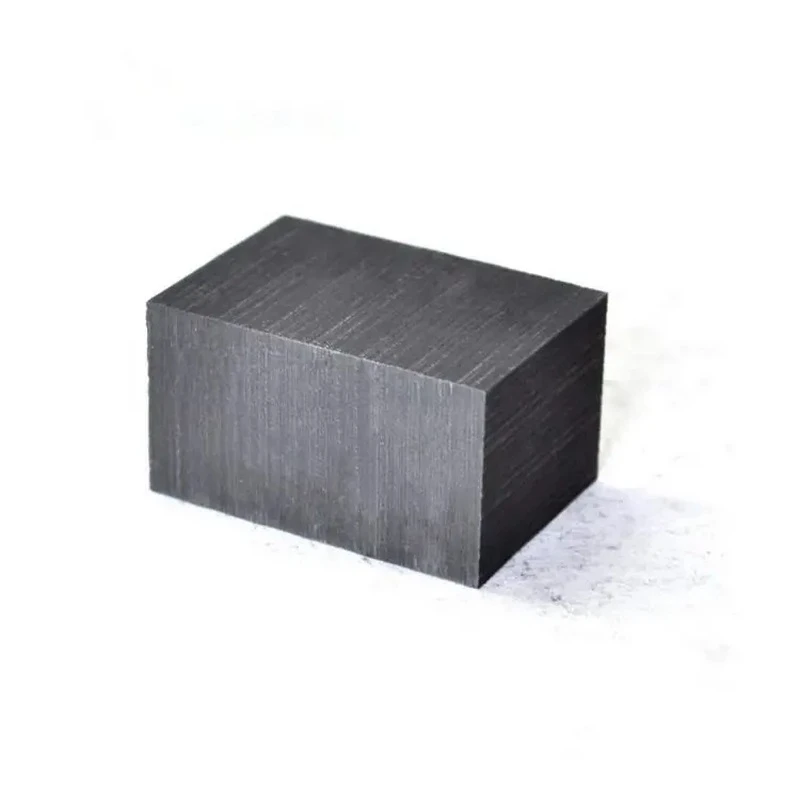
Conversely, machining copper electrodes presents more challenges. Copper is more difficult to machine smoothly. It requires specific tool geometries, lower cutting speeds, and often specialized coolants to prevent built-up edges on the cutting tool and achieve a good finish. The process is slower, leading to higher labor and machine time costs for electrode fabrication. While copper can be cut into intricate shapes, it generally takes longer and requires more care than machining graphite. This ease of machining is a major advantage of graphite and a significant factor driving the shift from copper to graphite in many EDM shops. You can machine the material safely and efficiently, getting your electrode ready for the EDM machine much faster.
Which Electrode Wears Less: Graphite or Copper in EDM Applications?
Electrode wear is a critical factor in EDM, impacting accuracy, the number of electrodes needed, and overall job time. Generally, graphite electrodes exhibit lower wear rates compared to copper, particularly during roughing operations which use higher currents. Graphite’s extremely high sublimation point means it withstands the intense heat of the spark better than copper, which melts at a much lower temperature. This superior thermal resistance results in less wear on the graphite electrode, meaning it retains its shape for longer. This often allows a single graphite electrode to complete a roughing and semi-finishing operation where multiple copper electrodes might be required.
However, the situation can be more nuanced in finishing operations. Very fine-grained graphite electrodes offer excellent wear resistance even in finishing, but traditional wisdom sometimes favors copper electrodes for achieving the absolute finest finishes with minimal wear, especially when using positive polarity on the electrode and specific EDM machine settings. Furthermore, copper tungsten electrodes (an alloy, not pure copper) offer excellent wear resistance, particularly for intricate details, but come at a significantly higher cost. For most common EDM applications, especially those involving significant material removal, the lower wear rate of graphite electrodes translates into needing fewer electrodes (one or two electrodes instead of potentially a third or forth electrode to finish the job) and improved process stability. Graphite electrodes also tend to have more predictable wear patterns.
Can You Achieve Faster EDM Machining Speeds with Graphite or Copper Electrodes?
Achieving faster EDM machining speeds, often measured as Material Removal Rate (MRR), is a key goal for improving productivity. While copper’s higher electrical conductivity might suggest it should be faster, practical EDM experience often shows that graphite electrodes enable higher overall MRR, especially with modern EDM machine technology. Why? Because graphite’s superior thermal properties and wear resistance allow operators to use higher peak currents and longer on-times without excessive electrode wear or damage. Pushing a copper electrode too hard thermally can lead to rapid melting and deterioration, forcing operators to use more conservative settings.
Modern EDM power supplies are sophisticated enough to optimize the spark characteristics for different electrode materials. They can effectively leverage graphite’s ability to handle aggressive parameters, leading to significantly faster roughing and semi-finishing cycles compared to copper. While the absolute highest MRR might be theoretically achievable with copper under specific, wear-inducing conditions, the practical, usable MRR that balances speed with acceptable electrode wear is often higher with graphite electrodes. This ability to remove material faster without quickly destroying the electrode makes graphite electrodes a more productive choice for many jobs run on a CNC EDM machine. The direct flow of current can be managed more aggressively with graphite.
What About Surface Finish? Does Copper or Graphite Deliver Better Results?
The required surface finish on the final workpiece is a major factor in choosing between graphite or copper electrodes. Traditionally, copper electrodes were considered superior for achieving ultra-fine, mirror-like finishes. Copper’s structure allows it to produce a very smooth surface on the workpiece, especially during slow, fine-finishing passes often done with positive electrode polarity. For applications demanding the absolute highest polish, copper is often the preferred electrode material.
However, advancements in graphite manufacturing have closed this gap considerably. Modern, ultra-fine grain graphite electrodes (often made from isostatically pressed graphite) can achieve excellent surface finishes that are suitable for the vast majority of EDM applications. The achievable finish on the graphite depends heavily on the grain size and quality of the graphite material – the finer the grain, the smoother the potential finish. While copper might still hold a slight edge for true mirror finishes, high-quality graphite electrodes are used very successfully for molds and dies requiring fine textures and smooth surfaces. Often, the surface finish achievable with graphite should be as good or nearly as good as copper, while still offering benefits in wear and speed. For many jobs, the finish difference is negligible, making graphite’s other advantages more compelling.
Cost Considerations: Is Graphite or Copper the More Economical Electrode Material Overall?
Evaluating the cost-effectiveness of graphite vs copper electrodes requires looking beyond the initial material price. While the raw material cost for basic copper might be lower than for some grades of graphite, the total cost of using an electrode material involves several factors:
- Raw Material Cost: Copper is generally cheaper per pound/kg than high-quality graphite material. However, prices fluctuate, and premium graphite grades can be expensive.
- Electrode Machining Cost: Graphite machines significantly faster (3-5x) than copper. This drastically reduces labor and machine time costs for electrode fabrication, often offsetting the higher material cost of graphite.
- EDM Time Cost: Higher MRR achievable with graphite electrodes means less time spent on the EDM machine, reducing operational costs per part.
- Number of Electrodes: Graphite’s lower wear rate often means fewer electrodes are needed per job (one or two electrodes vs potentially 3 or 4 for copper). This saves on both material and machining costs for the additional electrodes. For example, needing a third or forth electrode to finish the mold adds significant expense if using copper.
- Handling/Machine Stress: Lighter graphite electrodes put less stress on the EDM machine‘s servos, potentially reducing maintenance needs, especially for large electrodes.
When all these factors are considered, graphite electrodes are often used because they frequently prove to be the more economical choice overall, despite a potentially higher initial material cost per unit weight. The savings in electrode fabrication time, reduced EDM cycle time, and the lower number of electrodes used typically outweigh the difference in raw material price for many EDM applications. It’s crucial for procurement professionals like Mark Thompson to analyze the total cost of ownership, not just the purchase price per kilogram, when making the chose – graphite or copper decision.
Choosing Wisely: When Should You Use Copper vs Graphite Electrodes for Specific EDM Tasks?
The optimal choice of electrode material depends heavily on the specific requirements of the EDM job. There’s no single "best" material for all situations. Here’s a general guideline:
Use Graphite Electrodes When:
- Speed and High MRR are Critical: For roughing and semi-finishing where removing material quickly is the priority.
- Complex Electrode Shapes are Needed: Graphite’s excellent machinability makes it ideal for intricate geometries.
- Low Electrode Wear is Essential: Especially for deep cavities or jobs requiring multiple parts with consistent dimensions.
- Large Electrodes are Required: Graphite’s light weight reduces stress on the machine.
- Cost-Effectiveness is Key: The overall savings in machining and EDM time often favor graphite.
- Good to Excellent Surface Finish is Sufficient: Modern graphite grades satisfy most finish requirements.
- Operating on modern EDM machines with advanced power supplies capable of optimizing graphite performance.
Use Copper Electrodes When:
- Ultra-Fine/Mirror Surface Finish is Paramount: Copper still holds an edge for the absolute highest polish requirements.
- Very Fine, Delicate Electrode Features: Copper’s toughness makes it less prone to chipping during handling or setup compared to brittle graphite.
- Specific Finishing Strategies: Some shops prefer copper for specific fine-finishing techniques or when using older EDM machine technology less optimized for graphite.
- Simple Electrode Geometries: If the electrode shape is very basic, the machining time advantage of graphite is less significant.
- Working with Copper-Tungsten: For applications needing extreme wear resistance in fine detail, though this is a more expensive alloy.
Ultimately, the decision requires evaluating the specific job’s priorities: Is it speed, surface finish, cost, complexity, or wear resistance? Understanding these trade-offs allows you to choose the right type of electrode for optimal results. Many shops keep both graphite and copper electrodes available, selecting the best electrode material on a job-by-job basis.
Beyond Performance: What Other Factors Influence the Graphite vs Copper Electrode Decision?
Beyond the core performance metrics like wear, speed, and finish, other practical factors influence the graphite or copper decision, particularly for international buyers like Mark Thompson sourcing from China.
- Supplier Reliability and Quality Control: This is paramount. As a manufacturer (like my company, producing high-quality graphite products), we understand the importance of consistent material properties. Mark’s concern about quality inspection and certifications (ISO standards, material specs) is valid. Reputable suppliers provide detailed material data sheets and maintain strict quality control from raw material sourcing to finished electrode. Occasional certificate fraud is a real risk, so vetting suppliers thoroughly is crucial. Partnering with established factories with transparent processes minimizes this risk. We ensure our High performance pre baked anode carbon block and electrodes meet rigorous standards.
- Communication: Mark’s pain point about inefficient communication is common. Working with a supplier who has responsive, knowledgeable sales and technical support fluent in English is vital. Clear communication prevents misunderstandings about specifications, delivery schedules, and payment terms. As Allen, I prioritize clear, direct communication with clients.
- Logistics and Lead Times: Shipment delays can cripple production schedules. Reliable logistics planning and realistic lead time estimates from the supplier are critical. The availability of graphite or copper stock and the supplier’s production capacity influence this. We maintain efficient production across our 7 lines to ensure timely delivery to the USA, Europe, and Australia.
- Material Handling and Safety: Machining graphite produces conductive dust, requiring effective dust collection systems for worker safety and to prevent shorts in machine electronics. Shops must be equipped to handle this. Copper machining produces chips, which are generally easier to manage but require proper coolant handling.
- Technical Expertise: While Mark is knowledgeable in sales, his lack of deep technical expertise highlights the need for a supplier who can offer guidance. Choosing the right grade of graphite electrode (e.g., UHP, HP, RP, or specific EDM grades like our Conductive graphite rod for electrodes) or copper electrode requires understanding the application. A good supplier acts as a partner, helping select the optimal electrode material.
These factors underscore the importance of choosing not just the right material, but the right supplier. A reliable partner provides quality graphite electrodes or copper electrodes, ensures smooth logistics, communicates effectively, and offers technical support, addressing the key concerns and pain points faced by international buyers.
Key Takeaways: Graphite vs Copper Electrodes
Choosing the right electrode material for your EDM machine is crucial for success. Here’s a quick summary of the key points comparing graphite and copper electrodes:
- Graphite Electrodes: Generally offer faster machining (electrode fabrication), higher material removal rates (MRR) in the EDM process, lower wear (especially in roughing), and are lighter weight. Ideal for complex shapes, speed-critical jobs, and often more cost-effective overall due to time savings. Require good dust control during machining.
- Copper Electrodes: Offer superior electrical conductivity and can achieve the finest surface finishes. They are tougher (less brittle) than graphite but are slower and more difficult to machine, leading to higher electrode fabrication costs. Can suffer from higher wear rates, especially under aggressive roughing conditions.
- Machinability: Graphite is significantly easier and faster to machine (3-5x).
- Wear Rate: Graphite generally wears less, requiring fewer electrodes per job.
- Speed (MRR): Graphite often allows for higher practical MRR on modern EDM machines.
- Surface Finish: Copper excels for mirror finishes, but high-quality graphite provides excellent finishes suitable for most applications.
- Cost: Graphite often has a lower total cost of use when machining time, EDM time, and the number of electrodes are factored in, despite potentially higher raw material costs.
- Application: The best electrode to choose – graphite or copper – depends entirely on the specific job priorities (speed, finish, complexity, cost, wear).
- Supplier Choice: Factors like quality control, communication, logistics, and technical support are as important as the material itself, especially when sourcing internationally.
Understanding these advantages and disadvantages empowers you to make informed decisions, optimizing your EDM applications for efficiency, quality, and profitability. Whether you use graphite or use copper, selecting the right type of electrode and partnering with a reliable supplier is key.
Post time: 04-14-2025